
Visit our community sponsor

Thanks:
0

Likes:
0
-

Yes, I love Technology
CV Joint Dissy made easy
For the ones you hammer apart only...
Sitting at the axle roulette table. Since I'm building from stuff like 08 Legacy chassis, 02 Impreza axle parts, 2000 female outputs trans, '02 EZ30D motor and a whole mix-mash of other pieces (there was no 'take home' donor), I guessed and ordered my 818S as 02-04 NA version. Axles with the kit = PN 80240, sporting 29 spline to 21 spline. My 02 inboard (trans side) are 29 spline as are the rears from the Legacy outer. The inner CV's are green, look un-rebuilt, I'd expected them to be 24 spline (only 'cause that's what FFR sent for an 02 project). FFR is sending some others should be 29-29 and then we'll see.
Taking CV's apart became déjà vu after awhile (6 in all & I've read much worse stories here).
It occurred to me - hammering on the housing to knock it off the shaft includes trying to accelerate the mass of the housing before anything else happens. Why not get things in motion first and let the shaft's inertia end the matter. Over all this has potential for less excitement. In fact after doing some, it gets to be kinda-fun! As always, care and prudence must be observed.
I did hammer the first couple joints out. Worked, but a lot of effort, increasing violence and dinging up edges, etc. Also good to have a range of medium to ridiculous sized hammers (I got) as things escalate.
By the way, after the big glops are removed with a rag, etc., grease is easier removed with solvent and small brush than wiping and pleading.
The easy ways:
1) Rig press plates or equivalent vertical "stoppers", put a catcher below for the drive shaft. "Drop" (you may have to help a bit) the assembly down so the housing stops and shaft can keep going. Start gentle, it won't take much probably. You could simulate this setup with some pipe and bits if you don't have a press.
2) Why spend time setting up anything. If your workbench has the mass (3/8 x 2' x 5' steel plate here), just hold with towels, be ready to slow the shaft, and "bring it home" to the end of the workbench. Unless you have recalcitrant shaft clips, you are done in about 5 seconds per. Use the towels, glove transfers a lot of shock, trust me.
as in:
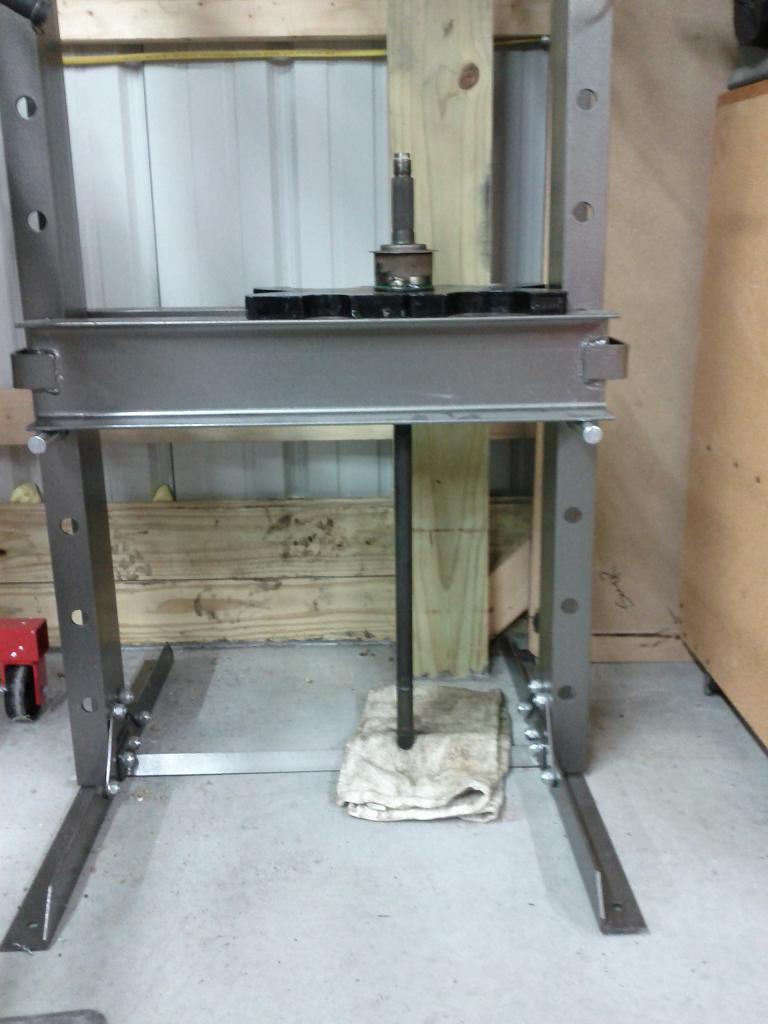
and
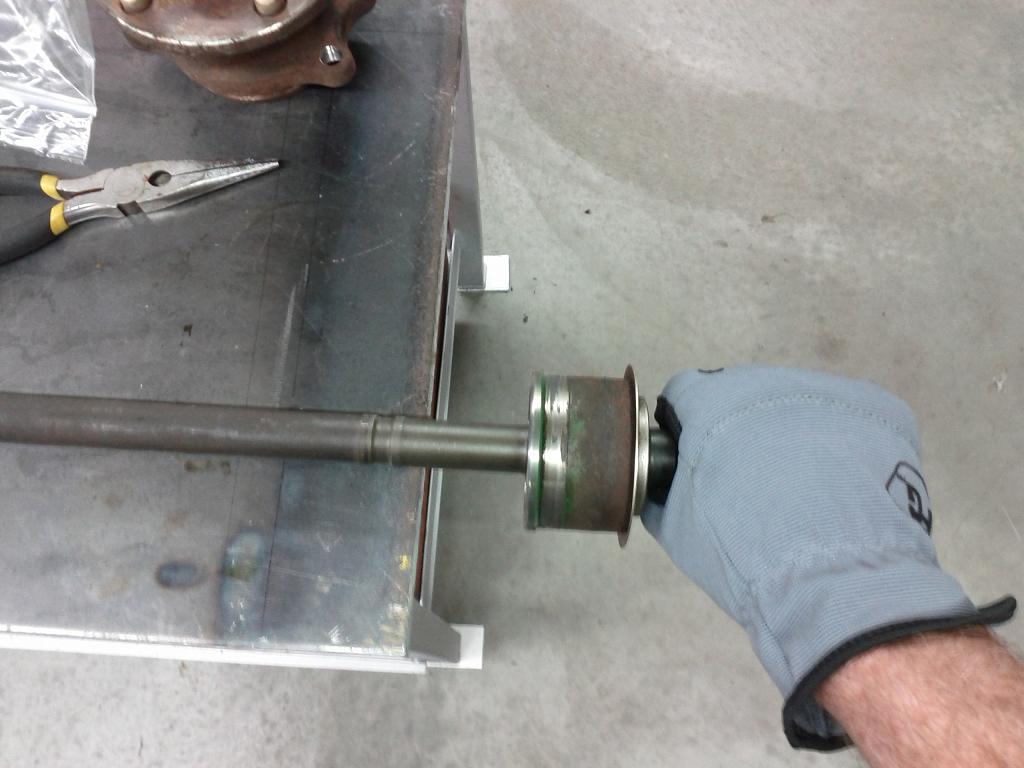
If you really want to be nice, slip something under the axle so the table edge doesn't catch the boot grooves.
Last edited by aquillen; 07-19-2017 at 05:42 PM.
-

Yes, I love Technology
Reading older threads the other day, found at least two posts where others described this same axle drop disassembly method, one even used the HF press exactly like this. Got a feeling I must have saw that a while back and it stayed in the back of my mind. Takes the wind out of my sails. But never hurts to say some things again. So hard to find things in these posts/threads it seems.
Posting Permissions
- You may not post new threads
- You may not post replies
- You may not post attachments
- You may not edit your posts
-
Forum Rules

Visit our community sponsor