-
Pinion angle - I think I've got it but please check me
OK, so I've read through all the recent discussions about pinion angle, as well as Karlos' excellent writeup. I think I have an understanding of the concept and the goals, but given the importance of getting this right I wouldn't mind being sanity-checked that all's good. My setup is as follows: Gen 2 coyote, TKO 600 with 3/4" of spacers under trans mount, and IRS. My measurements are as follows:
Engine/trans: -0.5* (tail of trans is angled down)
Driveshaft: +0.5* (driveshaft is angled up, i.e., rear is higher than front)
IRS: +1.0*
I'm coming up with OA1 (operating angle 1: trans to DS) of 1.0* and OA2 (DS to IRS) of 0.5*. Therefore, I think I'm satisfying all three conditions:
1) operating angles within 1* of each other
2) maximum operating angle at either end = 3*
3) minimum continuous operating angle at least 0.5*
My only concern, and I'm not sure this is a valid concern, is that the engine and IRS are not co-planar, i.e., one is angled down while the other is angled up. If all three conditions above are met, is that an issue or am I OK?
Also, those with similar setups, do these numbers sound similar to what you have? The reason I ask is that I had initially measured the other day with my digital angle finder and was getting slightly different numbers (that put me out of spec) but that device was a little suspect as it had been accidentally dropped a few times and not all segments in the display were working. Before I started messing with the setup I figured I'd spend the $30 for a new digital angle finder. The new unit arrived today, and the above numbers are what I got from it.
Thanks,
John
MkIV Roadster build: Gen 2 Coyote, IRS, TKO600. Ordered 10/24/18. Delivered 1/29/19. Engine installed 8/8/21. First start 9/12/21. First go-kart 9/17/21. Off to paint 4/11/22. Back from paint 12/30/22.
Build thread here.
-
Senior Member
Not a concern with IRS. The angles don't change as the pinion doesn't move. Don't get why this is sooo over thought
Mrk III, 331 stroker, Borla stack injection, T5, 3:55 IRS, Power steering and brakes. Kleiner body & paint
-
Damn, you were soooooo close to providing a helpful response without being snarky, but you snuck it in right at the end there. good on ya.
MkIV Roadster build: Gen 2 Coyote, IRS, TKO600. Ordered 10/24/18. Delivered 1/29/19. Engine installed 8/8/21. First start 9/12/21. First go-kart 9/17/21. Off to paint 4/11/22. Back from paint 12/30/22.
Build thread here.
-
Post Thanks / Like - 0 Thanks, 3 Likes
-
Seasoned Citizen
John, is the imaginary center line through pinion shaft as viewed from the side angled up at the front 1-deg from horizontal? If so, you're good to go and I wouldn't expect any issue on a performance street car.
Dart Little M 406" SBC 800 HP N/A & 1,100 HP on nitrous, 2-spd Powerglide with trans brake, 6,000 RPM stall converter, narrowed Moser 88 3.90:1 spool with 35-spline gun-drilled axles & Torino bearings, custom parallel four-link, custom tube chassis & roll cage NHRA certified for 8.5-sec (only two FFR Hot Rods have this cert).
33 Hot Rod Super Pro Drag Racer Build:
33 HR NHRA Cert Roll Cage Build
-
Senior Member
John are using any of Forte's spacers? FWIW (427/fixed motor mounts) I ended up with three of them to get me within specs. I struggled a little with the Tremec app and really do not know if I am dead nuts 100% on but felt like I was close enough. Figured I would feel some type of vibration during my first go-kart. So far (knock on wood) it has been fine over 1k miles now, smooth as butter, no vibrations or leaks.
-
They say a picture is worth a thousand words, but this one is pretty lousy so it may be worth nothing... but here goes:
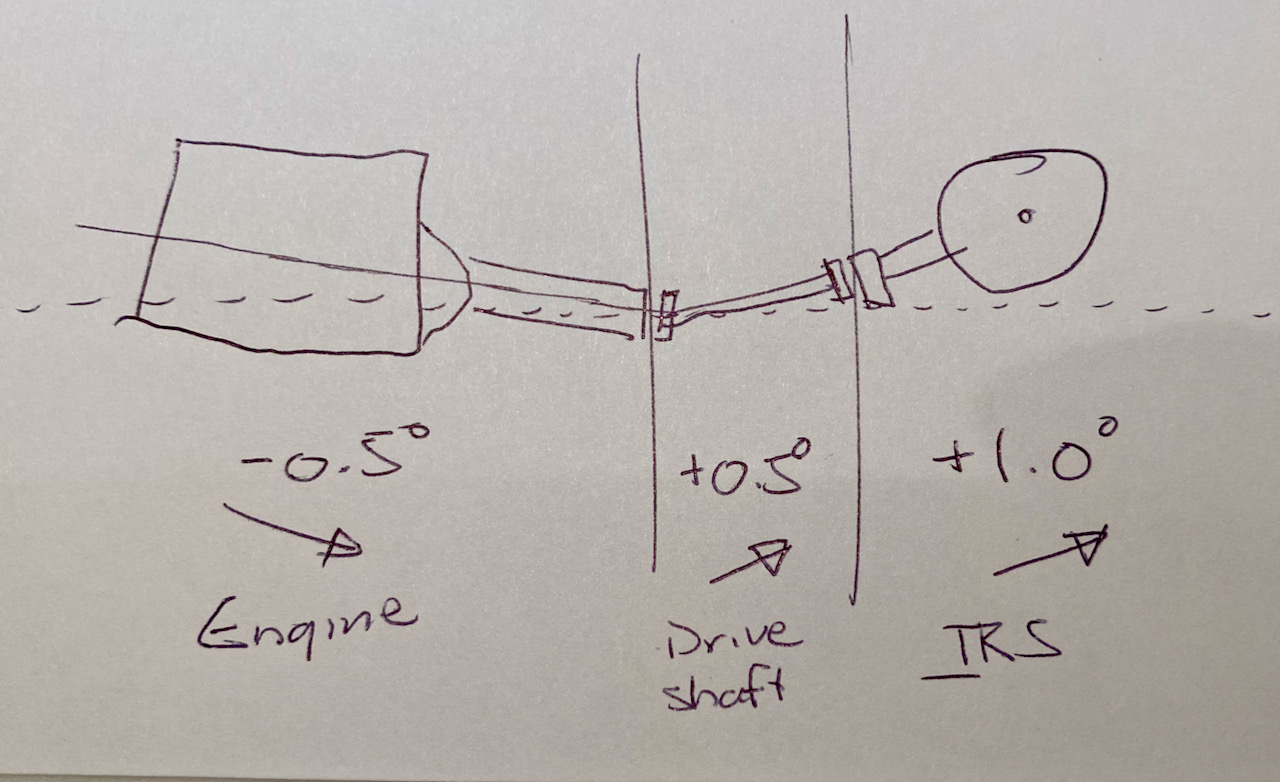
Travis, yes, I have three of Forte's spacers for a total of 3/4" of spacers under the tail of the transmission.
MkIV Roadster build: Gen 2 Coyote, IRS, TKO600. Ordered 10/24/18. Delivered 1/29/19. Engine installed 8/8/21. First start 9/12/21. First go-kart 9/17/21. Off to paint 4/11/22. Back from paint 12/30/22.
Build thread here.
-
Post Thanks / Like - 0 Thanks, 1 Likes
Fman liked this post
-
Senior Member
That is not good. The engine/trans should be parallel to the diff. OTOH, your 3/4 shim is very common, and it is off such a small amount that I don't expect it to cause a problem.
FFR MkII, 408W, Tremec TKO 500, 2015 IRS, DA QA1s, Forte front bar, APE hardtop.
-
Post Thanks / Like - 1 Thanks, 0 Likes
JohnK thanked for this post
-
Senior Member
On a street driven car, that should be ok, might be a concern on a track car at 150mph. The angle of the driveshaft isn't a concern, it's how close to parallel the output of the transmission and the pinion of the differential are. The closer the better, but 100% isn't necessary, anything under 3-4* will work on a street car. Remember the drive shaft on a street car isn't likely to spinning at very high rpm's for long periods of time.
pinion_angle_bad_angles.PNG
Mrk III, 331 stroker, Borla stack injection, T5, 3:55 IRS, Power steering and brakes. Kleiner body & paint
-
Post Thanks / Like - 0 Thanks, 2 Likes
-
Seasoned Citizen
Want to echo what Craig said. It's the worst case scenario as far as setting up a drivetrain. You'll want to correct that before driving the car.
Dart Little M 406" SBC 800 HP N/A & 1,100 HP on nitrous, 2-spd Powerglide with trans brake, 6,000 RPM stall converter, narrowed Moser 88 3.90:1 spool with 35-spline gun-drilled axles & Torino bearings, custom parallel four-link, custom tube chassis & roll cage NHRA certified for 8.5-sec (only two FFR Hot Rods have this cert).
33 Hot Rod Super Pro Drag Racer Build:
33 HR NHRA Cert Roll Cage Build
-
Post Thanks / Like - 1 Thanks, 0 Likes
JohnK thanked for this post
-
I had a chance to try out a few different options this afternoon, and here are the results.
First I tried adding three hardened washers in addition to the 3/4" of spacers under the trans mount. This brought the engine into the same inclination as the IRS but the operating angle between the DS and IRS was too great (3.3*).
I then removed one washer so I had 3/4" of spacers and two hardened washers on each bolt, and had the results shown below. Overall this looks like the best compromise to me, but I'd love some feedback. The engine/trans and IRS are pointed in the same direction (engine +0.2*, IRS +0.9*), my operating angles are both <3* (1.8* and 2.5*), and the difference between the two operating angles is less than one degree (0.7*). Does this look like a reasonable setup?
Last edited by JohnK; 08-18-2021 at 09:20 AM.
MkIV Roadster build: Gen 2 Coyote, IRS, TKO600. Ordered 10/24/18. Delivered 1/29/19. Engine installed 8/8/21. First start 9/12/21. First go-kart 9/17/21. Off to paint 4/11/22. Back from paint 12/30/22.
Build thread here.
-
Senior Member
I think you will be fine.
FFR MkII, 408W, Tremec TKO 500, 2015 IRS, DA QA1s, Forte front bar, APE hardtop.
-
Senior Member
Ideally you want driveshaft within .5* to differential. Your pic #1 with 3 washers gets you there.
Build 1: MKIV #7275 Gen 2 Coyote TK600, IRS 3.55 2020 Graduated
Build 2: Gen3 65 Coupe: Arrived June 2024. Gen 2 Coyote, T56, IRS 3.55
-

Originally Posted by
nuhale
Ideally you want driveshaft within .5* to differential. Your pic #1 with 3 washers gets you there.
This is where I'd love some feedback. With the three washers I get the pinion angle (difference between OA1 and OA2) to 0.5* but OA2 (driveshaft to IRS angle) is >3* so that doesn't seem ideal to me. From what I understand, it's better to have the slightly larger pinion angle of 0.7* with the two washers in order to get both operating angles less than three degrees. But then again, I've never done this before and I'm just going by everything I've read here and elsewhere.
MkIV Roadster build: Gen 2 Coyote, IRS, TKO600. Ordered 10/24/18. Delivered 1/29/19. Engine installed 8/8/21. First start 9/12/21. First go-kart 9/17/21. Off to paint 4/11/22. Back from paint 12/30/22.
Build thread here.
-
Seasoned Citizen
John, now that you have your pinion shaft and trans output shaft closer to parallel, you’ll probably be happy with the result of either of the two set-ups in your latest sketch. But let me share with you some thoughts.
On a parallel, zero-degree phasing driveshaft like most of us run; I’d accept more operating angle to reduce the variance in operating angles between the two u-joints. The difference between the two joints has more impact on vibration than operating angles (up to a point).
If I recall, Spicer bases their u-joint life on 5,000 RPM operation at 3-degrees of operating angle. Increase the operating angle more than 3-deg and life expectancy diminishes and critical speed also diminishes but your driveshaft is so short that I suspect your critical speed is far grater than your driveshaft will ever see. I’ve run much more than 3-deg operating angles on lifted short wheelbase 4X4 vehicles and accepted the greater wear as it’s not really that big a deal on special vehicles that don’t clock hundreds of thousands of miles.
But driveshaft vibration has the potential to be a much more serious problem than accelerated u-joint wear. And u-joints that are not operating at the same angle are operating out of phase. The more variance, the more out of phase they are and out of phase conditions create torsional vibrations (twice per revolution) which are destructive. A driveshaft experiencing torsional vibration is speeding up and slowing down twice on every revolution. That’s increasing the load and reducing it twice every revolution. Think of it like flooring the gas and lifting as fast as you can repeatedly for each mile you drive. How long before you would see broken parts? Therefore, I place a higher priority on reducing the variance between the two operating angles than the degree of operating angle.
This video has been around and is a great demo of out of phase operation: https://www.youtube.com/watch?v=Idk3BVDVHq4
Dart Little M 406" SBC 800 HP N/A & 1,100 HP on nitrous, 2-spd Powerglide with trans brake, 6,000 RPM stall converter, narrowed Moser 88 3.90:1 spool with 35-spline gun-drilled axles & Torino bearings, custom parallel four-link, custom tube chassis & roll cage NHRA certified for 8.5-sec (only two FFR Hot Rods have this cert).
33 Hot Rod Super Pro Drag Racer Build:
33 HR NHRA Cert Roll Cage Build
-
Thanks NAZ! That's extremely helpful. If you were me what would you do in my shoes? Would you put the third washer back in? Would you try a fourth washer to get the variance even smaller, even if it results in OA's close to 4*?
MkIV Roadster build: Gen 2 Coyote, IRS, TKO600. Ordered 10/24/18. Delivered 1/29/19. Engine installed 8/8/21. First start 9/12/21. First go-kart 9/17/21. Off to paint 4/11/22. Back from paint 12/30/22.
Build thread here.
-
Seasoned Citizen
John, I'm meticulous (used to be a tool room machinist) so I would do whatever required to get the perfect drive train angles, including modifying the chassis and fabricating parts if that what it took. So you can probably guess what direction I'd push you.
Given no other choice, I'd accept 4-deg or more operating angle to get zero degrees variation between the trans output shaft and the pinion shaft (i.e. both parallel) and I want that on both the vertical and horizontal planes. Preventing an out of phase condition is that important to me.
Operating angles rob power so my ideal operating angle for a street car is 1-deg, in a race car I shoot for zero degree as this is the most efficient angle for transmitting torque. But everything is a matter of compromises.
Have fun with your build and don't take shortcuts -- this is supposed to be a fun learning experience. A couple extra days building will be forgotten the first time you drive the car and everything is simply perfect.
Dart Little M 406" SBC 800 HP N/A & 1,100 HP on nitrous, 2-spd Powerglide with trans brake, 6,000 RPM stall converter, narrowed Moser 88 3.90:1 spool with 35-spline gun-drilled axles & Torino bearings, custom parallel four-link, custom tube chassis & roll cage NHRA certified for 8.5-sec (only two FFR Hot Rods have this cert).
33 Hot Rod Super Pro Drag Racer Build:
33 HR NHRA Cert Roll Cage Build
-
Post Thanks / Like - 0 Thanks, 1 Likes
-
Senior Member

Originally Posted by
JohnK
Damn, you were soooooo close to providing a helpful response without being snarky, but you snuck it in right at the end there. good on ya.
I know, that guy cracks me up! He can't help himself.
Matt
FFR Complete Kit, Coyote, Tremec TKX, 3.73 IRS, power steering, 18" Halibrands, Wilwood brakes, Gas-N pipes + header, Viking blue color
Roadster Build Time Tracker
-
Senior Member

Originally Posted by
JohnK
I had a chance to try out a few different options this afternoon, and here are the results.
First I tried adding three hardened washers in addition to the 3/4" of spacers under the trans mount. This brought the engine into the same inclination as the IRS but the operating angle between the DS and IRS was too great (3.3*).
I then removed one washer so I had 3/4" of spacers and two hardened washers on each bolt, and had the results shown below. Overall this looks like the best compromise to me, but I'd love some feedback. The engine/trans and IRS are pointed in the same direction (engine +0.2*, IRS +0.9*), my operating angles are both <3* (1.8* and 2.5*), and the difference between the two operating angles is less than one degree (0.7*). Does this look like a reasonable setup?
John, I was about to PM you on this but thought others might benefit as well so posting here. Can you please let me know how you are measuring the angles so precisely? I have a digital angle finder, but how are you mounting it to the components to get such accurate measurements?
Matt
FFR Complete Kit, Coyote, Tremec TKX, 3.73 IRS, power steering, 18" Halibrands, Wilwood brakes, Gas-N pipes + header, Viking blue color
Roadster Build Time Tracker
-
Hi Matt,
Good question. I'm using this digital angle finder. They're sold under countless different brands on Amazon and they're most likely all made in the same factory in China but I made myself feel better by buying a name brand so I can believe it's more accurate. Here's how I'm measuring each angle:
1) Engine/trans - I measure in two places. First, I measure on the face of the crank pulley. Second, I have a rigid metal ruler that I lay flat against the bell housing block off plate and have it project down below the bell housing, and use that as a representation of the vertical plane of the rear of the engine to measure against.
2) Driveshaft - this one is pretty easy. Just attach the magnetic angle finder to the driveshaft. The only tricky bit is making sure it is attached the same way each time (and obviously avoid setting it on one of the welds on the ends of the DS). This particular angle finder has a notch on each face so that it can fit on pipes and whatnot. If you're not careful it's easy to set it on the DS in such a way that it's not seated squarely in that notch, which will throw off the readings. Just make sure it's fully seated in the notch (if your DAF has a notch) and that it's hanging perpendicular.
3) IRS - this one is the trickiest, IMO. It would be easy if the driveshaft wasn't mounted but with the DS in place I had to really play around with different methods before I found a way that yielded repeatable results. I measure in three places. First, I lay the thin edge of the rigid ruler against the exposed edges of both the pinion flange itself and also the driveshaft adapter and let the ruler project down and set the DAF on it to measure. I also set the DAF on the bottom face of the pinion flange. I wasn't sure if this would be an accurate reading but it turns out that it yields the same reading as the other two and it's much easier/faster. In any case, once you've got your IRS number it's not going to change so you don't need to keep re-measuring it.
For all of these readings I will take multiple measurements, completely removing the DAF and setting it back in place again. Only when I get a repeatable number 2-3 times in a row do I trust it, and for the engine/trans and IRS where I'm measuring in multiple places I won't trust it unless I get the same reading in both places. I've also found that it takes 2-3 seconds for the DAF to "settle" and give an accurate number.
I hope that helps. I'm happy to snap some photos of what I'm describing if that's helpful.
-John
MkIV Roadster build: Gen 2 Coyote, IRS, TKO600. Ordered 10/24/18. Delivered 1/29/19. Engine installed 8/8/21. First start 9/12/21. First go-kart 9/17/21. Off to paint 4/11/22. Back from paint 12/30/22.
Build thread here.
-
Post Thanks / Like - 1 Thanks, 0 Likes
-
NAZ, thank you! I agree with you 100%. I do this for fun, and to learn. I fully expect to re-do things multiple times until they're done to my satisfaction. I re-did my brake lines multiple times before I was happy with them. Short-cutting things or accepting "good enough" is just going to irritate me down the road, as I will always wish I'd put in the time and effort to get it as good as I possibly could (within the limitations of my skills.) I don't understand this mindset by some of "it's good enough, why are you wasting your time?" If it's seen a a waste of time, why are they bothering building a car in the first place?
On the driveline angles, a couple more questions. My skills preclude me from re-doing IRS or engine mounting locations, so I'm sort of limited to what I can do by adding/subtracting shims under the the transmission. Within that constraint, should I keep adding spacers until I get the engine/trans as close to perfectly parallel to the IRS, even if it means I end up with operating angles of 5* - 6*? Extrapolating out, it seems that each washer I add adds 0.2* degrees to the engine/trans angle and roughly 1* to the operating angles. So if I were to go with 5 washers I would expect to see the engine/trans at 0.8* (vs. the IRS at 0.9*) and operating angles somewhere around 5*. If I understand you correctly, in this scenario I'm sacrificing some power and u-joint longevity in exchange for vibration reduction. Given that I'm not going to be putting 100's of thousands of miles on this car, that's probably an OK compromise.
Sorry to keep bombarding you with additional questions. I really do appreciate you sharing your knowledge (and hopefully this thread is useful to others).
-John
MkIV Roadster build: Gen 2 Coyote, IRS, TKO600. Ordered 10/24/18. Delivered 1/29/19. Engine installed 8/8/21. First start 9/12/21. First go-kart 9/17/21. Off to paint 4/11/22. Back from paint 12/30/22.
Build thread here.
-
Seasoned Citizen
John, I tend toward calculated risk and love to experiment so I'm going to try and answer this not as a recommendation but as what I might try if faced with your situation. Some of the things I do are not in alignment with conventional wisdom, therefore, should not be considered as "conventional" and agreed on by any peer group. Increasing the operating angle will decrease the life of the u-joint just as increasing the speed above 5,000 RPM will decrease the life. You can find charts that show that relationship and the speed reduction required to get the same life for a given operating angle.
I have run operating angles in excess of 8-degrees and know of others that have run 12-deg or more and claim no vibration issues. Shorter shafts are more forgiving than longer so there is not a one size fits all maximum operating angle that I can give you as a not to exceed limit. There is also a double cardan option that I can use as a work around if I get into vibration from extreme operating angles so I'm not afraid to experiment and push the envelope. So given your application and based on my experience, I'd likely try as much as a 6-degree operating angle as I've run more than that on a longer driveshaft than yours without issue. But then, this is experimenting and not something I'd "recommend" as I don't tend to recommend things that I'm not 100% confident will work.
If I could get the trans output shaft and the pinion shaft within .1-degree of being parallel I'd accept a 6-degree operating angle on a street car. But if I could get within .1-degree I could not help myself from getting to exactly parallel, but maybe I'm OCD. And if that didn't work out I know I could get myself out of any problem I created. I still remember what an engineer told me when I was training at the Ford Engineering Center, "if you can make it worse -- you can make it better". So don't be afraid to experiment. Also keep in mind that when setting up all these angles you are typically not limited to just shimming the trans mount, raising or lowering the engine mounts might also be an option if that helps gain a preferred attitude.
John, don't give up until you get as close to perfection as practical within your knowledge, skill, and what you've been given to work with. As builders, we're responsible for the performance and reliability of these cars and we are the ones that have to most control over the finished product. I think you're going about your build the right way.
Dart Little M 406" SBC 800 HP N/A & 1,100 HP on nitrous, 2-spd Powerglide with trans brake, 6,000 RPM stall converter, narrowed Moser 88 3.90:1 spool with 35-spline gun-drilled axles & Torino bearings, custom parallel four-link, custom tube chassis & roll cage NHRA certified for 8.5-sec (only two FFR Hot Rods have this cert).
33 Hot Rod Super Pro Drag Racer Build:
33 HR NHRA Cert Roll Cage Build
-
Post Thanks / Like - 2 Thanks, 0 Likes
-
Thanks NAZ. It's very helpful for someone inexperienced like me to understand boundary conditions and which "rules" are flexible and which are inviolable when experimenting, so I appreciate your insights and voice of experience. I'll play around some more and report back.
I did think briefly about modifying the engine mount spacers to drop the front of the engine but as it currently sits, the lowest point of the oil pan is only ~1/16" higher than the bottom of the 4" tubes and I don't think I want the oil pan to be the low point when going over a speed bump.
MkIV Roadster build: Gen 2 Coyote, IRS, TKO600. Ordered 10/24/18. Delivered 1/29/19. Engine installed 8/8/21. First start 9/12/21. First go-kart 9/17/21. Off to paint 4/11/22. Back from paint 12/30/22.
Build thread here.
-
Seasoned Citizen
John, many others have concerns with the oil pan extending beyond the frame rails. Not saying that's wrong but I don't have the same worries and it did not prevent me from lowering my engine below my frame rails. Frame rails provide very limited protection of the pan and a 1/2" one way or the other is not a deal breaker for me if I need to move the engine around in the chassis. Just another point of view...
Dart Little M 406" SBC 800 HP N/A & 1,100 HP on nitrous, 2-spd Powerglide with trans brake, 6,000 RPM stall converter, narrowed Moser 88 3.90:1 spool with 35-spline gun-drilled axles & Torino bearings, custom parallel four-link, custom tube chassis & roll cage NHRA certified for 8.5-sec (only two FFR Hot Rods have this cert).
33 Hot Rod Super Pro Drag Racer Build:
33 HR NHRA Cert Roll Cage Build
-
OK, I've now added a total of 6 washers (0.59" total thickness), along with the original 3/4" of Forte's spacers. This gives me +0.9* angle on the engine/trans to match the +0.9* angle on the IRS. The driveshaft angle is -5.4*, which gives me operating angles on both u-joints of 6.3*. I think I'm calling this done!
Thank you NAZ for teaching a masterclass on driveline angles.
MkIV Roadster build: Gen 2 Coyote, IRS, TKO600. Ordered 10/24/18. Delivered 1/29/19. Engine installed 8/8/21. First start 9/12/21. First go-kart 9/17/21. Off to paint 4/11/22. Back from paint 12/30/22.
Build thread here.
-
Senior Member
-
Post Thanks / Like - 0 Thanks, 1 Likes