-
To Weld or Not to Weld.....Ford 8.8 Welded Tubes?
Ok so there looks to be several posts on this in the past but looking for some fresh (recent) input.
I am getting ready to pull my rear end for a rebuild/repaint and trying to decide if I should take the time to weld the axle tubes. Ill be putting new gears in and stepping up to 31 spline for piece of mind.
If I were to weld the axle tubes, there's no "cost" as I would do this myself with plenty of experience in the welding and fab area. Have tigs and migs, etc. Am aware of the nuances, distortion control, stress cracking, correct filler metals to use, etc., of welding cast steel.
Looks like if I were to weld the tubes, the banana bracket would have to be ground out to create clearance for the weld between the tube and the pumpkin. So that would kill the powder coating on the bracket which is a bummer.
Question is with a planned build of 5-550hp in the future is it worth it or would it be overkill/waste of time?
I never plan to run slicks or run down a 1/4 mile. Has never interested me.
I may run auto-x one day but that's just a mild interest at this point and may never do it.
I am just not a fan of doing things twice but if unnecessary I am not a fan of wasting time
As always, appreciate the feedback guys!
Last edited by Doc76; 11-27-2024 at 11:29 AM.
-
Not a waxer
Weld the banana bracket to the tube because that will fail first. Nothing to lose by welding the tubes to the center while you’re at it but not really absolutely necessary IMO.
Jeff
-
Post Thanks / Like - 1 Thanks, 0 Likes
Doc76 thanked for this post
-
I'm running a 408 making 545HP in a spyder GT with a 3 link. I broke it running low 10's but the problem wasn't the tubes it was the banana bar itself. It didn't slip on the tube, it bent into an S. I straightened it and boxed it and it's holding up well. But there goes the powder coat...
-
Post Thanks / Like - 1 Thanks, 0 Likes
Doc76 thanked for this post
-

Originally Posted by
Jeff Kleiner
Weld the banana bracket to the tube because that will fail first. Nothing to lose by welding the tubes to the center while you’re at it but not really absolutely necessary IMO.
Jeff
Do you or perhaps anyone that's done this happen to have a photo of this scenario?
Looks like on the FFR Moser 8.8 they eliminate the bolted sections all together and weld the passenger side of the banana bracket to the tube and the drivers side of that bracket gets welded to the pumpkin.
I am guessing that if I were to do this I could eliminate at least the lateral brace that goes from that bolted banana bracket to the front flange on the passenger side?
-

Originally Posted by
Presdough
I'm running a 408 making 545HP in a spyder GT with a 3 link. I broke it running low 10's but the problem wasn't the tubes it was the banana bar itself. It didn't slip on the tube, it bent into an S. I straightened it and boxed it and it's holding up well. But there goes the powder coat...
If you're able could you share a picture of your fix?
while I have it all out that would be an easy one to nail off.
-
Senior Member
This is a friends banana bracket after years of autocrossing on Hoosiers.
Wades 3 link.jpg
He ordered a new one and reinforced it before installing. Sorry I don't remember if he welded it to the axle or not. I 'think' he had welded it to the casting but not the tube. After his died I pulled mine and reinforced it. I boxed in a lot of the main banana and also added an additional tube from near the top down to where it bolts to the web in the diff casting.
IMG_20150902_091800903.jpg
IMG_20150902_141638084.jpg
I did not weld mine to the axle. I do tig but didn't/don't have enough knowledge about welding mild steel to a casting and was concerned about warping the axle tube.
Last edited by CraigS; 11-28-2024 at 09:37 AM.
FFR MkII, 408W, Tremec TKO 500, 2015 IRS, DA QA1s, Forte front bar, APE hardtop.
-

Originally Posted by
CraigS
This is a friends banana bracket after years of autocrossing on Hoosiers.
Wades 3 link.jpg
He ordered a new one and reinforced it before installing. Sorry I don't remember if he welded it to the axle or not. I 'think' he had welded it to the casting but not the tube. After his died I pulled mine and reinforced it. I boxed in a lot of the main banana and also added an additional tube from near the top down to where it bolts to the web in the diff casting.
IMG_20150902_091800903.jpg
IMG_20150902_141638084.jpg
I did not weld mine to the axle. I do tig but didn't/don't have enough knowledge about welding mild steel to a casting and was concerned about warping the axle tube.
Thanks for sharing
I think based on your guys recommendations I’ll box that bracket in when I weld up the tubes.
Did you weld your tubes to your pumpkin?
Seems to be mixed reviews on what filler to use. (309L, 8-60, ER70s-6 and I’ve read a few others)
-
Not a waxer

Originally Posted by
CraigS
This is a friends banana bracket after years of autocrossing on Hoosiers.
Wades 3 link.jpg
He ordered a new one and reinforced it before installing. Sorry I don't remember if he welded it to the axle or not. I 'think' he had welded it to the casting but not the tube. After his died I pulled mine and reinforced it. I boxed in a lot of the main banana and also added an additional tube from near the top down to where it bolts to the web in the diff casting.
IMG_20150902_091800903.jpg
IMG_20150902_141638084.jpg
I did not weld mine to the axle. I do tig but didn't/don't have enough knowledge about welding mild steel to a casting and was concerned about warping the axle tube.
Craig,
Is that Wade's? I think I remember he was also able to taco the "banana" portion on another occasion. But of course he was able to break the unbreakable
Still miss him...
Jeff
-
Senior Member
Yes it is. Like you, I surely miss him. It happened at an SCCA AX at FedEx field. He and I worked a bit w/ several ratchet straps so he could drive it home. He lived maybe 30 min beyond me. So as soon as we had a workable solution I took off for home. My daily driver at the time was a 2011 Tacoma. So I got home and contacted another FFR bud who had a trailer. Plan was if the rig came apart, he would call me to give his location, I'd grab the trailer, pick him up and get him to his house. Fortunately the straps worked well enough that we didn't need the trailer.
FFR MkII, 408W, Tremec TKO 500, 2015 IRS, DA QA1s, Forte front bar, APE hardtop.
-
Any value to add 9” ends to the axle tube and lateral bracing from the ends to the pumpkin?
Couple foxbody guys locally suggested it for higher HP capability but not sure bracing or 9” ends is necessary with ~550hp or just overkill and extra $
It’s a mod I can do myself which is why I am considering it.
-

Moderator
FWIW, I added another brace after hearing of lateral failures. You'll read more about this elsewhere, but add this into the mix.
2024-10-02 08.37.53.jpg
James
FFR33 #997 (Gen1 chassis, Gen2 body), license plate DRIVE IT says it all!
build thread
My build: 350SBC, TKO600, hardtop, no fenders/hood, 32 grill, 3 link, sway bars, 355/30r19
Previous cars: GTD40, Cobra, tubeframe 55 Chevy, 66 Nova, 56 F100
-
Post Thanks / Like - 1 Thanks, 0 Likes
Doc76 thanked for this post
-

Originally Posted by
RoadRacer
FWIW, I added another brace after hearing of lateral failures. You'll read more about this elsewhere, but add this into the mix.
2024-10-02 08.37.53.jpg
Good to know. Easy to add. Just so I understand, the banana bracket can fail at times (so folds over or?)
Local guys are doing this too but running way more HP than I’ll ever run but easy for me to add. Just not sure if it’s unecessary.
IMG_1104.jpg
Last edited by Doc76; 12-02-2024 at 01:55 PM.
-

Moderator
Here is the original issue; https://thefactoryfiveforum.com/show...anhard-Failure
Most/all of these problems seem to appear when you start cornering fast, with a lot of grip. You'll notice that my fix stops the panhard mount or banana bracket from being removable independently. But that's fine; I balanced that with the need for a simple, quick fix.
If I was just driving this normally, I wouldn't bother.
James
FFR33 #997 (Gen1 chassis, Gen2 body), license plate DRIVE IT says it all!
build thread
My build: 350SBC, TKO600, hardtop, no fenders/hood, 32 grill, 3 link, sway bars, 355/30r19
Previous cars: GTD40, Cobra, tubeframe 55 Chevy, 66 Nova, 56 F100
-
Post Thanks / Like - 1 Thanks, 1 Likes
Doc76 thanked for this post
-

Moderator
I should probably add that I haven't welded any of the original pieces discussed. I added two braces though - the welded one above, and also this one (which IMO is the most important one)
https://www.vpmcobras.com/3linkbrace.htm (the first one).
James
FFR33 #997 (Gen1 chassis, Gen2 body), license plate DRIVE IT says it all!
build thread
My build: 350SBC, TKO600, hardtop, no fenders/hood, 32 grill, 3 link, sway bars, 355/30r19
Previous cars: GTD40, Cobra, tubeframe 55 Chevy, 66 Nova, 56 F100
-

Originally Posted by
RoadRacer
I should probably add that I haven't welded any of the original pieces discussed. I added two braces though - the welded one above, and also this one (which IMO is the most important one)
https://www.vpmcobras.com/3linkbrace.htm (the first one).
Noted thanks
I plan to box in the front and back of the banana bracket. I’ll probably make the bracing boltable though, either to tabs on the axle tube or down to the mount where you welded yours.
Good grief that’s crazy I just read that. Seems to me that a lot could be gained from gusseting that shock mount to the axle tubes like in this pic
IMG_1114.jpg
Last edited by Doc76; 12-02-2024 at 04:16 PM.
-
Post Thanks / Like - 0 Thanks, 1 Likes
-

Originally Posted by
RoadRacer
I should probably add that I haven't welded any of the original pieces discussed. I added two braces though - the welded one above, and also this one (which IMO is the most important one)
https://www.vpmcobras.com/3linkbrace.htm (the first one).
Do you have any pictures of the VPM braces?
The link is just an HTML verbiage file without images. I also Google-searched their site and get the same link without pictures. Love to see what these are.
I found some chopped up PhotoBucket pics online but tough to see. From what I can tell this is a really nice option. Hopefully still available cause I’m not a fan of welding the banana bracket to the rear end.
IMG_1134.png
Last edited by Doc76; 12-02-2024 at 11:32 PM.
-

Moderator
It’s the shorter one in this photobananabrace.jpeg
James
FFR33 #997 (Gen1 chassis, Gen2 body), license plate DRIVE IT says it all!
build thread
My build: 350SBC, TKO600, hardtop, no fenders/hood, 32 grill, 3 link, sway bars, 355/30r19
Previous cars: GTD40, Cobra, tubeframe 55 Chevy, 66 Nova, 56 F100
-
Post Thanks / Like - 1 Thanks, 0 Likes
Doc76 thanked for this post
-

Originally Posted by
Presdough
I'm running a 408 making 545HP in a spyder GT with a 3 link. I broke it running low 10's but the problem wasn't the tubes it was the banana bar itself. It didn't slip on the tube, it bent into an S. I straightened it and boxed it and it's holding up well. But there goes the powder coat...
Are you able to share a picture of what you ended up doing?
-
Anyone installed or considered a brace kit like this?
https://www.youtube.com/watch?v=GXcExFJZoAg
I believe if fit correctly, it could gusset the passenger shock mount to address that weak point and at the same time could enable removal of the square tube from the bottom of the banana bracket to the pumpkin because the hoop running below the pumpkin could be coped into the bottom of the banana bracket to double as that brace. I would of course per Jeffs recommendation still stitch weld the banana bracket to the axle tube
Interested to hear thoughts on this.
Last edited by Doc76; 12-03-2024 at 11:10 AM.
-
Senior Member
This is just another bump-steer issue. If this was a drag racing car, then yes, otherwise just weld the banana bracket and move on.
Not sure I would take any advice from the guy in the video, as he doesn't even know what he is welding. That is NOT cast iron, but cast steel.
Mrk III, 331 stroker, Borla stack injection, T5, 3:55 IRS, Power steering and brakes. Kleiner body & paint
-

Originally Posted by
rich grsc
This is just another bump-steer issue. If this was a drag racing car, then yes, otherwise just weld the banana bracket and move on.
Not sure I would take any advice from the guy in the video, as he doesn't even know what he is welding. That is NOT cast iron, but cast steel.
For sure thanks Rich
I was more interested in the method of bracing than anything. The fab and welding work is dead simple for me. Just want to only do this once
Do you have a preferred method to addressing the twisting of the banana bracket due to lateral force or just what guys above have been suggesting?
-
Not a waxer
Really, unless you plan on doing some serious autocross, drag or track time ON SLICKS what you're talking about is overkill. I welded the banana bracket to the axle and then proceeded beat the daylights out of my Mk3 doing all three running on R comps and never had any issues or broke or bent anything. Not to discourage you if you really want to do it just because you can but don't feel like it is absolutely a necessity.
Jeff
-
Post Thanks / Like - 1 Thanks, 0 Likes
Doc76 thanked for this post
-
Senior Member
I didn't have an issue on my old car, but it wasn't big power. I think just welding the bracket to the tube and to the center section is enough unless you plan on doing a bunch of drag racing with slicks. You'll spin the tires first if they are street tires. You can have all the HP in the world, but the tires have to stick. I have about 400hp, running on the old style IRS with Avon tires, it'll spin them before breaking.
Mrk III, 331 stroker, Borla stack injection, T5, 3:55 IRS, Power steering and brakes. Kleiner body & paint
-
Post Thanks / Like - 1 Thanks, 0 Likes
Doc76 thanked for this post
-
You have mentioned a couple times that the fab and welding is no big issue, if that's the case do it before you install the rear end, and you have an almost, bullet proof rear end set up.
-
Post Thanks / Like - 0 Thanks, 1 Likes
-
For those of you that welded the banana bracket in, any words of advice?
About the only picture I didn’t get is the position of the bracket with the car sitting in the tires. It’s now in the air with the axle at full drop.
I’ve placed several witness marks around it.
Did you guys that welded it, cut off the bolts, narrow up the bracket pad at all?
Once I weld the axle tubes it doesn’t look like there’s much wiggle room to hog out the inner radius of the banana bracket to clear the weld between the pumpkin and the axle tube.
And with the vent right there, seems the bracket pad has to be narrowed up a bit.
Also, when welding the banana bracket on, can a guy remove the lower sqr tube running diagonally up to the front of the pumpkin or do you guys leave it?
Seems it serves very little structural advantage once the banana bracket is welded.
Any pictures of how guys are welding these in that have/will last some time would be appreciated.
IMG_1168.jpg
Last edited by Doc76; 12-03-2024 at 10:46 PM.
-
Senior Member
All you are doing is stitch welding around the tube, not necessary for a continuous weld, leave the brace on, leave the bolts alone. In fact, DO NOT continuous weld on the tube, good way to warp it.
Mrk III, 331 stroker, Borla stack injection, T5, 3:55 IRS, Power steering and brakes. Kleiner body & paint
-
Post Thanks / Like - 1 Thanks, 0 Likes
Doc76 thanked for this post
-
Not a waxer
As Rich said, leave the bolts as is. Also leave the square tube. In fact do not remove it or change anything, just weld it as it sits. The purpose of welding it is simply to prevent it from rotating on the axle tube therefore weld only the front half of the two piece bracket that way if the banana portion ever bends (not likely) it can be unbolted to remove it. I flipped your photo over so that it's oriented as if you're looking at it from above and indicated where to weld:
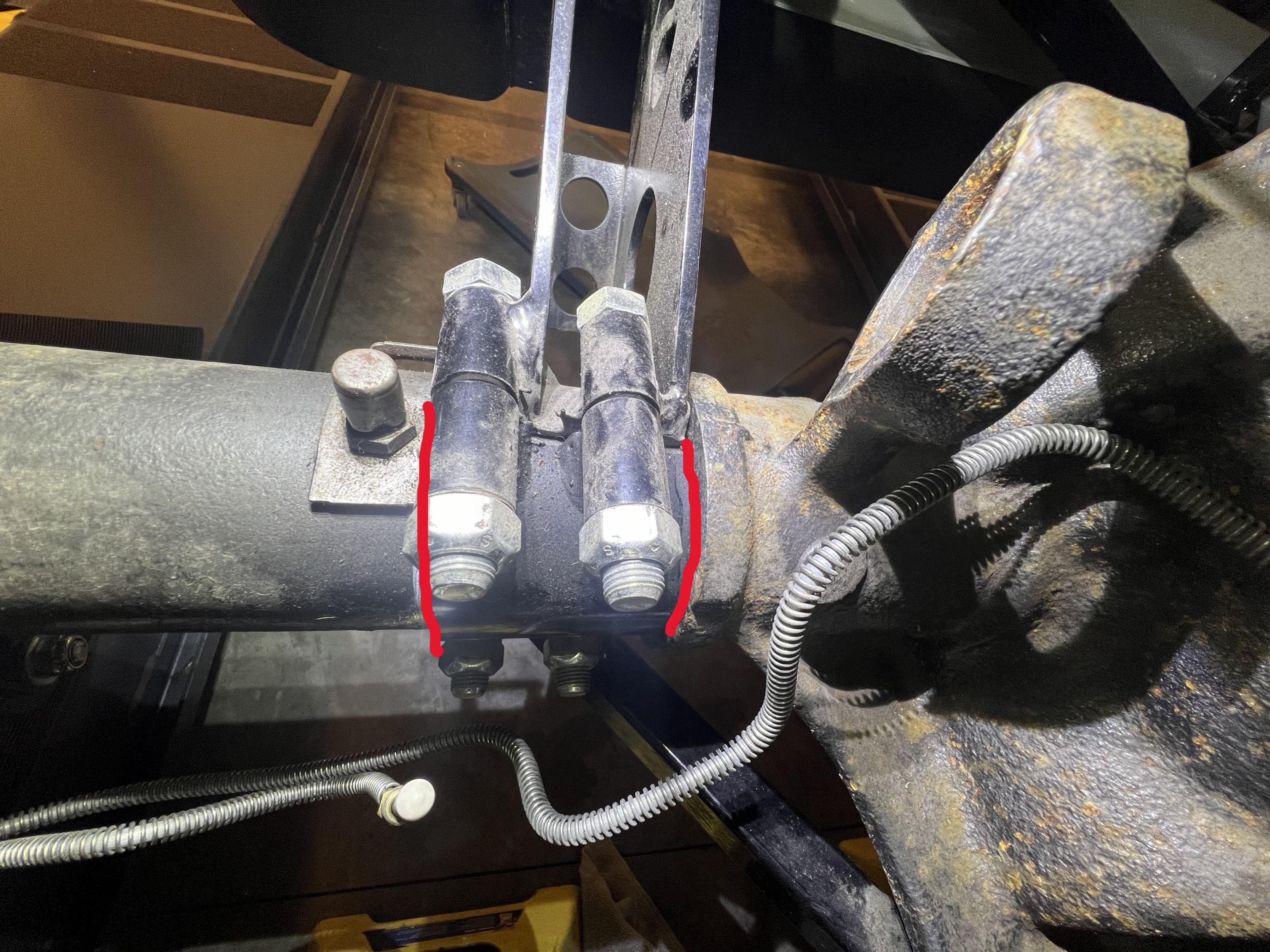
doc banana.jpg
-
Post Thanks / Like - 1 Thanks, 0 Likes
Doc76 thanked for this post
-
Would there be any downside to the VPM 3-link brace kit as opposed to welding the banana bracket on?
I would think maintaining the adjustability is the main benefit however I don’t really see anyone using these wondering if there’s a reason why other than the $115.
IMG_1200.jpg
Last edited by Doc76; 12-04-2024 at 10:43 AM.
-
Not a waxer

Originally Posted by
Doc76
I would think maintaining the adjustability is the main benefit...
IMG_1200.jpg
There is no adjustment to the banana bracket. The benefit of the VPM piece is that it is used in lieu of welding.
Jeff
-
Post Thanks / Like - 1 Thanks, 0 Likes
Doc76 thanked for this post
-

Originally Posted by
RoadRacer
FWIW, I added another brace after hearing of lateral failures. You'll read more about this elsewhere, but add this into the mix.
2024-10-02 08.37.53.jpg
Any chance you could tell me what your distance is from the mount to the sway bar mount?
I plan to gusset the shock mount to the axle tube for good measure and would like to assure should I choose to add a sway bar, my gusset doesn’t interfere. Looks like there might be ~2-ish inches?
I circled in green
IMG_1216.jpeg
-
Found this one posted ~4-5 years ago
https://www.ffcars.com/threads/besid...3-link.641846/
All the more reason I'll be reinforcing mine
-
Managed to get the rear end out of the car today and gutted it. Also cut off the donor shock mounts. Next up, weld axle tubes. Have to fab a jig first though.
I can see why some guys have suspension failures too. So much undercut, craters at critical stress points and an astonishing amount of weld porosity in every weld I ground. I’ll definitely be doing some minor bracing.
IMG_1297.jpgIMG_1296.jpgIMG_1294.jpg
-
Any suggestions on how best to fit the banana bracket back into place ones the axle tubes are welded?
My concern is the bracket is currently fitted on the tube right up against the pumpkin. This aligns the lateral brace to the OEM hole ok as when I pulled the bolt out the arms is slightly out of alignment to the hole already.
My concern is once I have a weld in the way around the axle tube, the bracket is already made of, what I would say is too thin of material (1/8”), and if I cope out the bracket to clear the weld and stay in the same spot, the bracket will not have enough material to maintain any sort of structural integrity.
Alternatively If I move the bracket over to clear that weld it moves the lateral tube well out of alignment of the hole up front on the pumpkin as well as will move it too close to the axle vent tube.
IMG_1301.jpgIMG_1299.jpegIMG_1302.jpegIMG_1298.jpgIMG_1300.jpeg
Any advice on past similar experiences would be appreciated
Last edited by Doc76; 12-15-2024 at 01:50 PM.
-
Senior Member
Good grief. Bolt the thing in place, beat it with a hammer till the bolts go in, spot weld in a couple of places and you're done. This isn't rocket science or precision work. This isn't an engine assembly, an 1/8" or even a 1/4" left-right-up or down makes no difference, you've been posting repeatedly over & over about something that takes a 1/2 hr or less to do.
Mrk III, 331 stroker, Borla stack injection, T5, 3:55 IRS, Power steering and brakes. Kleiner body & paint
-
Lol really a hammer? (Good grief is right)
You and I build things not quite the same
I don’t have a 1/4”. Lucky if I even have 1/8”. But you would know that if you actually took the time to look at the pictures and read the question.
For sure not rocket science but a little planning goes a long way and then the hammers not required.
Thanks again for your oh so positive feedback Rich.
Quality
Merry Christmas Rich.
Last edited by Doc76; 12-15-2024 at 04:50 PM.
-
Senior Member
Yes thats right, a hammer. How many have you built? I have my 3 that I did, plus helping a bunch of friends work on theirs. Been doing FFR's for 20yrs, and worked on cars, trucks and farm equipment for almost 60 yrs. I know for a fact that there are quite a few items on the these build that need the help of a hammer or other persuasion tools to fit. The bracket on my car fit terrible and needed the 'hammer' to knock some sense into it to fit, it's metal you bend it to fit if you have to. Ask how many builder had to "adjust" the suspension tabs to fit the control arms..
You ask for advice but don't want to follow it, so why ask. Again, how many posts for just this, when it was 5 bolts to install, and if it made you feel better, tack weld it. Don't worry I see you don't need my help, you need an aerospace engineer
Mrk III, 331 stroker, Borla stack injection, T5, 3:55 IRS, Power steering and brakes. Kleiner body & paint
-
Senior Member
Doc, I think you may be overthinking and trying to over build things. Are you planning high rpm launches on drag radials or taking up rock crawling with your roadster? A street driven roadster on, even the stickiest street tires, is very unlikely to hurt the rear end. If you try to accelerate hard enough to hurt it, you’ll most likely loose control and wrap yourself around a tree or power pole. That has happened too many times to people since I joined the forum.
If you really must reinforce things then, spot weld the axle tube to the pumpkin in four spots 90 degrees apart. Grind dimples into the inside edge of the banana bracket matching the location of your spot welds on the axle tube for clearance. Spot weld the bracket to the tube and the pumpkin. You are done!
Try not to wrap yourself around a tree
Norm
Mk4 base kit 7721, 331 Stroker, Holley Sniper EFI, Wipers, Heater, Whitby Soft Top, Drop trunk mod and more
-
Post Thanks / Like - 1 Thanks, 0 Likes
Doc76 thanked for this post
-
Senior Member
I wish I had a better view but this is my rear end.
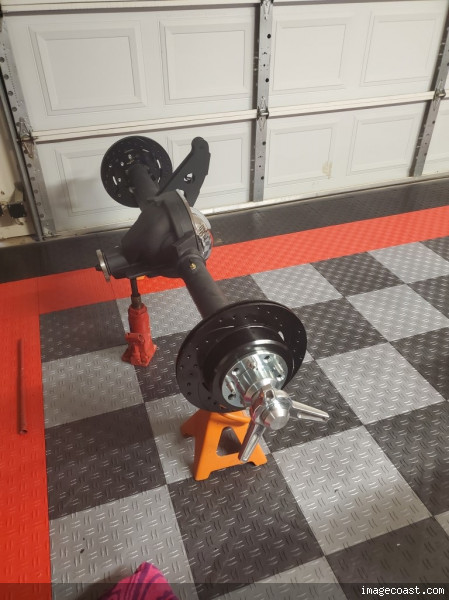
I bought it from Forte, he had a new narrow 8.8 in stock so I took it. I got the banana bracket from Factory Five ahead of my shipment and sent it to him to weld on. I noticed he completely removed the split bolt clamps and just welded the fabricated piece directly to the tube. To me either way would work if welding which I would strongly suggest.
-
Post Thanks / Like - 1 Thanks, 0 Likes
Doc76 thanked for this post
-

Originally Posted by
Doc76
Any suggestions on how best to fit the banana bracket back into place ones the axle tubes are welded?
My concern is the bracket is currently fitted on the tube right up against the pumpkin. This aligns the lateral brace to the OEM hole ok as when I pulled the bolt out the arms is slightly out of alignment to the hole already.
My concern is once I have a weld in the way around the axle tube, the bracket is already made of, what I would say is too thin of material (1/8”), and if I cope out the bracket to clear the weld and stay in the same spot, the bracket will not have enough material to maintain any sort of structural integrity.
Alternatively If I move the bracket over to clear that weld it moves the lateral tube well out of alignment of the hole up front on the pumpkin as well as will move it too close to the axle vent tube.
IMG_1301.jpgIMG_1299.jpegIMG_1302.jpegIMG_1298.jpgIMG_1300.jpeg
Any advice on past similar experiences would be appreciated
I had this very conversation with a fella last night that had the axle tubes welded to the center section of his 8.8. I had the same concerns as you because when I picked up my rear housing from the shop that narrowed it, they welded the tubes to the center section... he said they do it all 8.8's.
The fella I spoke to sent some pics of the banana bracket bolted to his 8.8 that was ~1/4" away from the center section due to the weld bead. He notched out a small area of the bracket so the vent would screw into the axle tube. He has been driving his car since around 2008 IRRC and was not concerned about the slight misalignment. The hiem joints are able to compensate...
I also found a thread from several years ago where a fella was using an 8.8 that came from FRPP. Apparently, when FRPP sold 8.8 housings all of them had the tubes welded to the center section. One of the responders in the thread suggested grinding the weld bead away to the banana bracket would sit flush against the center section.
I am in the process of putting mine together and believe I am going to grind a little of the weld bead away and put a slight bevel on the banana bracket to get it a little closer to the center section and call it good... this 8.8 is already trying to kill me. So far, my sawzall broke while cutting off the quad shock brackets, then I had a puller literally break while pulling the pinion flange, and my press blew a seal while pressing the pinion bearing off the old pinion.
-
Senior Member
I have been sitting in the weeds watching this thread go on. If one accepts that some brackets function with clamp bolts only, one could say adding a weld is like a belt and suspenders.
But perhaps the anxiety is that welding both sides is the only solution to instill confidence.
There is another compromise. One can weld bracket to tube and on the other side braze bracket to housing.
Braze?? The Brits have brazed and silver soldered frames together. CI blocks are repaired with braze.
This has been paralysis through analysis.
jim
Last edited by J R Jones; 12-17-2024 at 11:41 AM.