-
02-09-2019, 10:46 PM
#161
Well, things have been a little trying lately, as I'm getting defective or wrong parts that I have to wait on. First off, I pulled the 'donut' out of the TKO600. Pretty easy to do, but you have to be careful not to grab on to the actual seal. I took some channel locks, locked on to the donut and it came right out. Needle nose pliers weren't cutting it. Looks something like this:
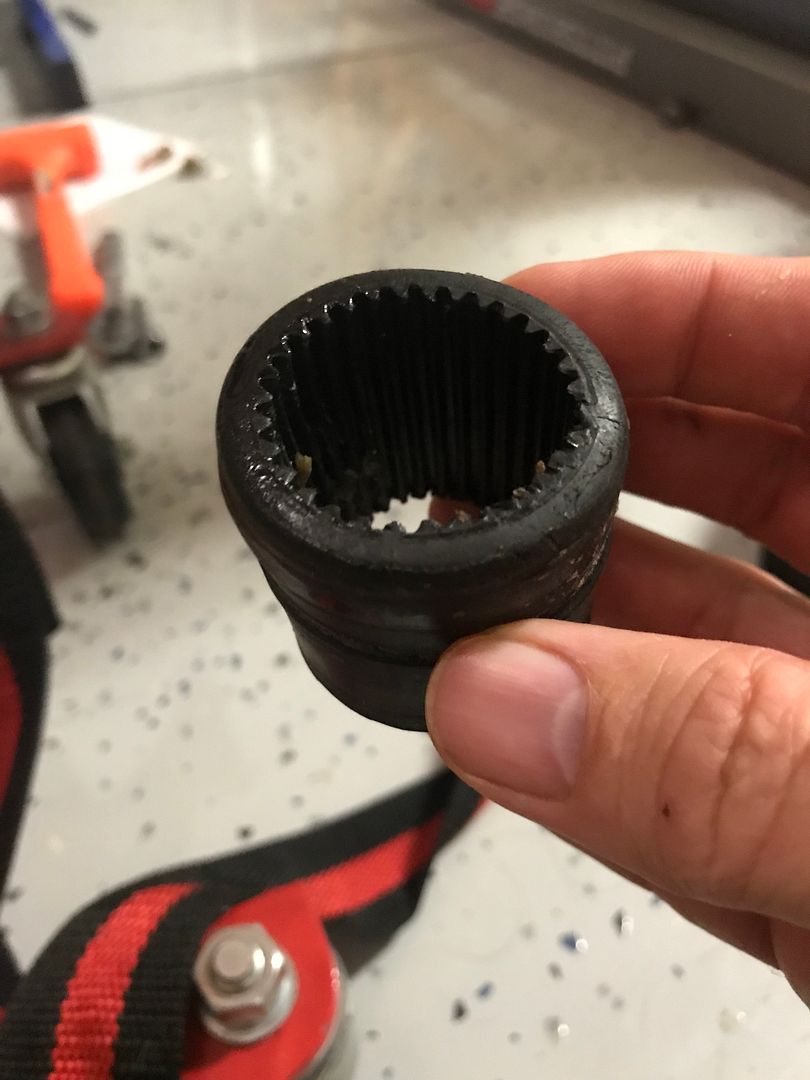
Once out, I inspected the seal, and you guessed it, was defective. The lip was rolled on one side and thanks to the forum advice, I swapped it out. The replacement for the TKO600 is Tremec #TCSJ1277. Funny thing was when I contacted Tremec, they were recommending a National part, and not a Tremec part. I read off the number from the old seal and they said "Oh yeah"...and sent me one almost next day, so good customer service on Tremec's part.
Very easy to swap out. I grabbed on the seal with a seal puller and popped out immediately. Pressed the new one back in flush with the housing by hand and then tapped it the rest of the way in with an electrical pipe fitting that I found at Home Depot and put a plastic 2" cap on the top. No sealer on the sides of the seal. As you can see in the pictures, the seal rests on a backstop inside the housing, so no guessing how far to drive in. When it stops, you're good.
Bad Seal
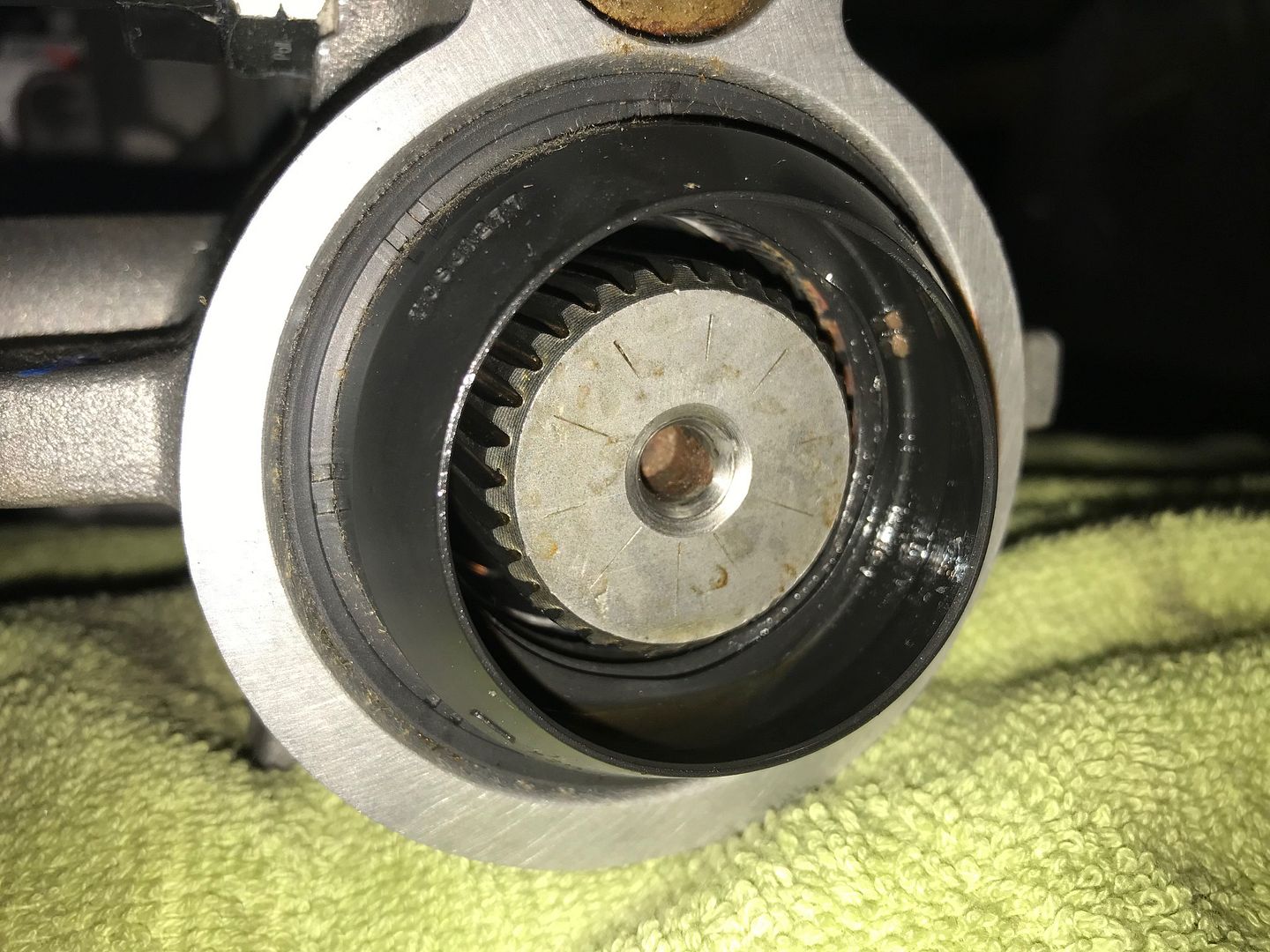
No Seal
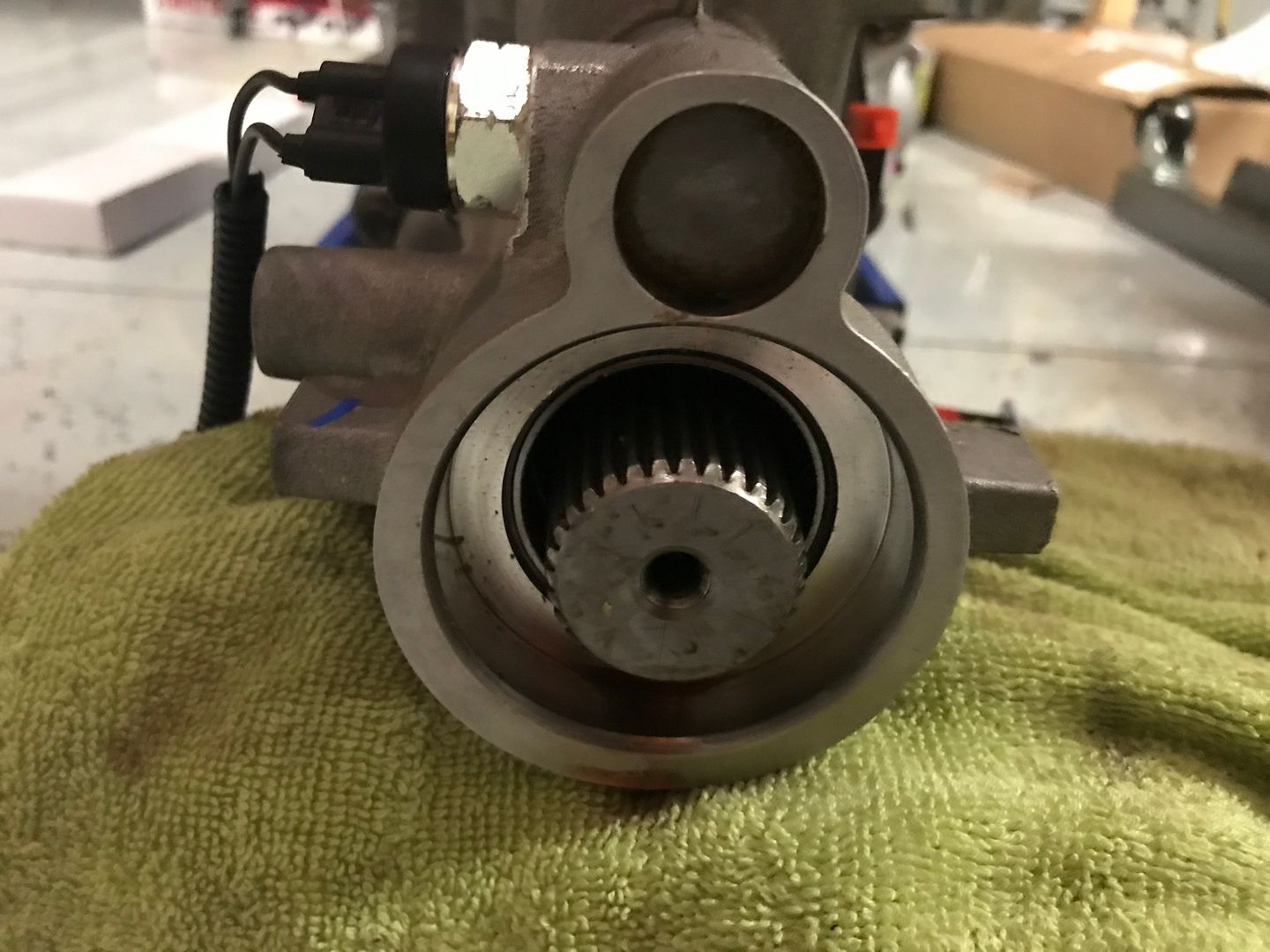
New Seal
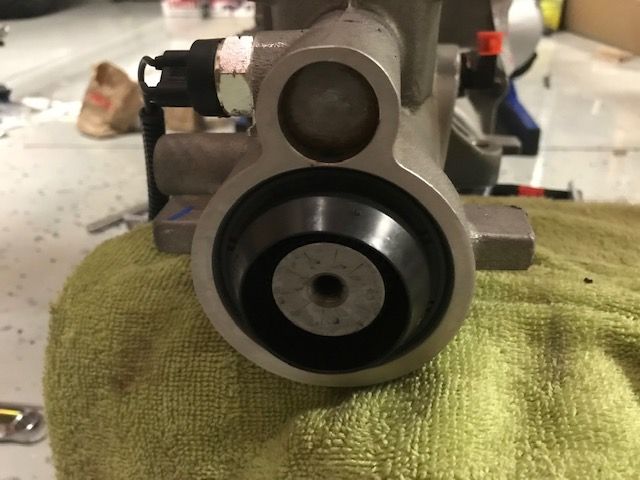
Seal Tapper (Home Depot #12320 - Halex 2" Electrical Tube)
Last edited by cv2065; 02-10-2019 at 10:32 PM.
-
Post Thanks / Like - 0 Thanks, 1 Likes
-
02-09-2019, 11:07 PM
#162
-
02-16-2019, 11:55 PM
#163
So, Mike Forte sent me a replacement bracket in record time. Thanks Mike! I'll get this other bracket sent back to you asap. Beautiful piece of aluminum billet and with the help of the forum, got this thing dialed in perfectly. I cut roughly 1-1/8" off of the slave cylinder push rod and have about 1/8" play from the TOB against the clutch fingers to bottoming out the slave. Bolts are tightened down to 30 ft/lbs.
I would have liked to have put another bolt into the fork bracket, but just not enough room. I'm sure it will hold just fine as designed. I will probably be proactive and just go ahead and add the 1" MC as so many have done.
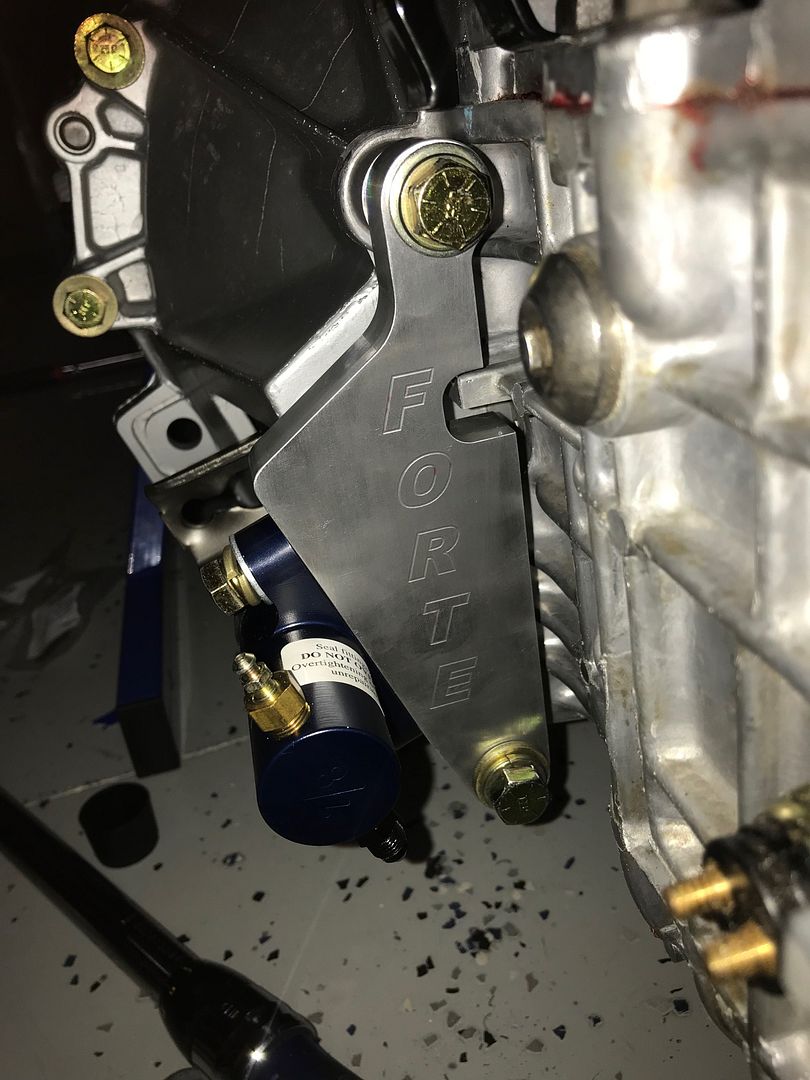
Last edited by cv2065; 02-17-2019 at 12:00 AM.
-
03-03-2019, 04:17 PM
#164
-
03-03-2019, 04:24 PM
#165
-
Post Thanks / Like - 1 Thanks, 1 Likes
-
03-03-2019, 04:28 PM
#166
-
Post Thanks / Like - 1 Thanks, 1 Likes
-
03-03-2019, 04:36 PM
#167
-
Post Thanks / Like - 0 Thanks, 1 Likes
-
03-03-2019, 04:37 PM
#168
-
03-03-2019, 04:41 PM
#169
Congratulations on the big milestone! It starts getting a lot more real once the engine is installed.
Dave
-
03-03-2019, 04:54 PM
#170
That's great, CV! Congratulations!
-
03-03-2019, 05:55 PM
#171
Looks good! Ready to go-cart at Easter?
-
03-03-2019, 06:39 PM
#172

Originally Posted by
Sigurd
Looks good! Ready to go-cart at Easter?
Thanks guys! I would definitely like to be go carting by Easter. You going to be back?
-
03-03-2019, 08:01 PM
#173
Awesome Job... That is a purrrrty motor.... Like Papa said, now it really starts getting/feeling real...
-
03-04-2019, 10:06 AM
#174
Looks great. Congrats. Your son will have a fun Monday telling everyone in school how he dropped the motor in the Cobra over the weekend!
-Steve.
-
03-05-2019, 09:18 AM
#175
Coming along nicely! engine looks great in there!!!!
-
04-07-2019, 09:24 PM
#176
Haven't updated in a while, but making steady progress.
Started on the sensors and engine wiring. With sensor installation, everything was straight forward except the oil pressure gauge. As has been mentioned, I needed to space the module out away from the side of the oil filter, so used the LMR oil pressure gauge extender, model #LRS-9278A. Paul had pointed this piece out in his build thread. It's a bit on the expensive side for what it is, but works and looks great.
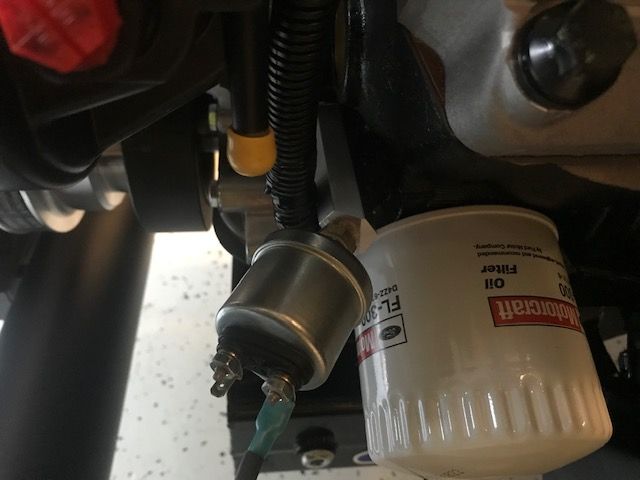
I had a goal of making as clean of an engine compartment as I could while running as few wire looms as possible. I've run the alternator, water temp, oil pressure, fan, coil and electric choke.
Most of the wiring was run in two looms, one on each side of the engine bay. Water temp, oil pressure and coil wiring came underneath the engine mounts, under the oil filter and up behind the power steering module. Alternator wiring ran underneath the engine mounts and up behind the alternator. All looks very clean and out of sight.
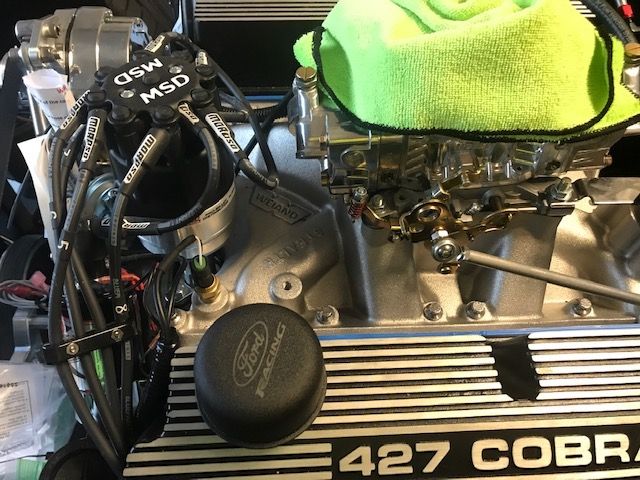
Electric choke and fan sensor wiring was a little more difficult to conceal since it is all on top of the intake. I just ran my loom on the inside of the fuel rail. Not ideal from a hiding standpoint, but looks OK. I may think about how to better hide it later. Maybe a 1/4" loom would work better.

Next up is getting the battery and starter wiring situated. I purchased a distribution block and will be running my battery to the block, then to the starter. I will also run the other two red wires to the distribution block. The blue solenoid wire will run directly to the starter. Just have to figure out the best place for the block.
Last edited by cv2065; 04-13-2019 at 08:46 PM.
-
04-13-2019, 09:00 PM
#177
Driveshaft went in with a bit of a struggle. There really is only one way that shaft will go in, and even then it almost looked like it was too much of an angle but with a little trans lube on the yoke, it eventually made it in. That little piece doesn't look like much, but I swear it weighed the same as a traditional driveshaft.
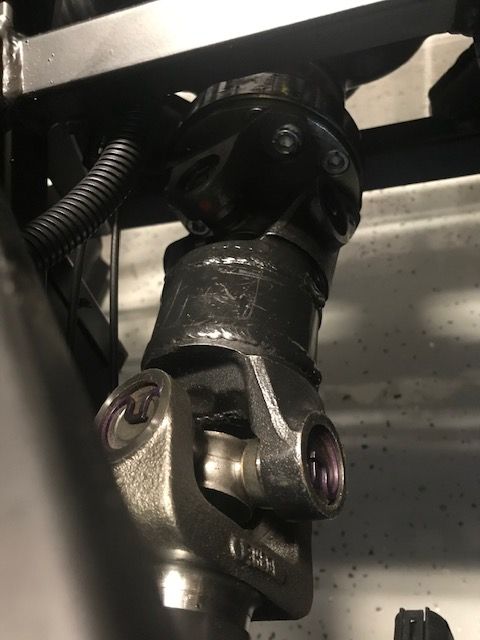
I had two sets of 12.9 cap screws for the driveshaft. One is 3/4" and the other 1". Was told by FFR, and David Williamson on the forum, that if you have an aluminum flange, then use the longer 1" bolts. Steel flange use the 3/4", as it is a shallower mount. If you use the longer 1" bolts with the steel flange, they almost secure flush, but still bottom out...maybe less than 1/16". I didn't use the 3/4", as I shaved off about a 1/8" off the longer bolts and used those as I wanted the longer thread engagement.
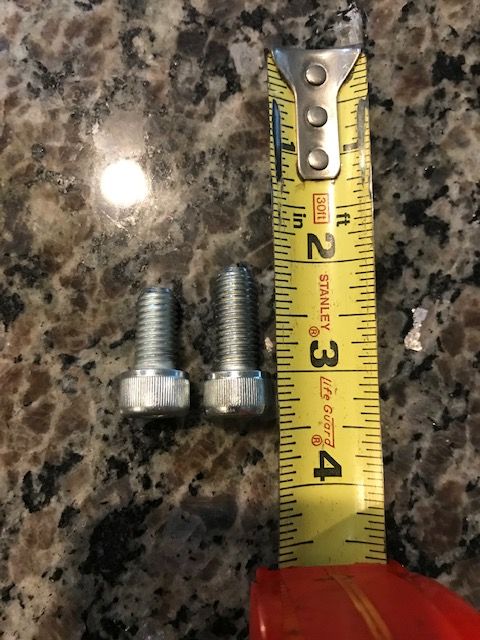
Bolts get tightened up to 70 ft/lbs. These need to be tightened up coming in from the top. If you try to tighten up from the bottom, you cannot get your torque wrench on it as there is not enough clearance, unless you have a really long extension. Blue loctite as prescribed in the instructions.
-
04-13-2019, 09:09 PM
#178
Next up was my radiator. This was another one of those projects that seem to linger around for a couple of weeks. My plan was to secure the radiator to the top FFR style, then use the Breeze lower support. All was going great until I got to the bottom support, and my radiator was about 3/4" too high, and the bottom support could not make contact with the radiator.
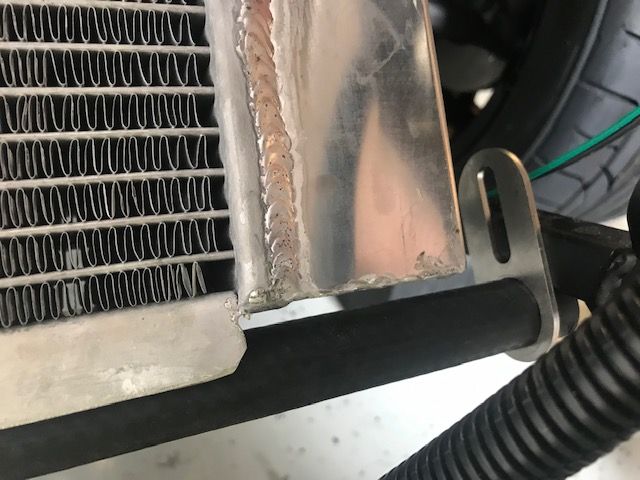
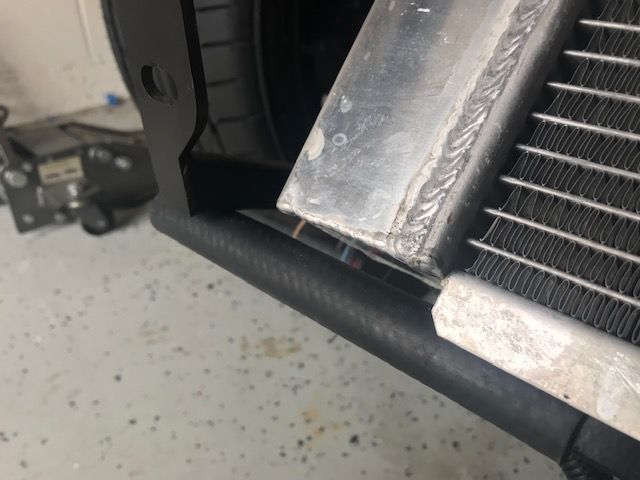
I contacted Mark from Breeze and he said that he runs into this every once in a while, and offered up the Breeze top hinge kit as a solution, as it drops the radiator down anywhere from 3/4" to maybe 1.5". Kit came in a couple of days.
I thought I'd get the maximum drop from the hinge, so I secured to the 3/4" tubes that are welded on to the frame. This unfortunately dropped the radiator too much, so per Breeze instructions, had to lop off the 2-3/4" tube pieces with a cut off wheel, clean them up with a grinder, repaint and secure the radiator right to the frame. Worked like a champ and is at the perfect angle of 58 degrees. I'm using the Replica Parts radiator panel so that requires a few more degrees from the traditional 51.
The Breeze upper hinge kit is nice in design, in that it uses two bolts that go all the way through the two top radiator flanges, as well as the fan, to provide overall support for the weight of the radiator. The aluminum flanges on the FFR radiator are thin and easily damaged, so you have to drill carefully.
One thing I did notice is that the passenger side 3/4" tube that is welded on to the frame is offset to the left. Although radiator is centered, the bolts are offset when you look at them which messes with my OCD. Carl and I were talking that maybe its for Mustang donor builds or another build all together, but who knows?
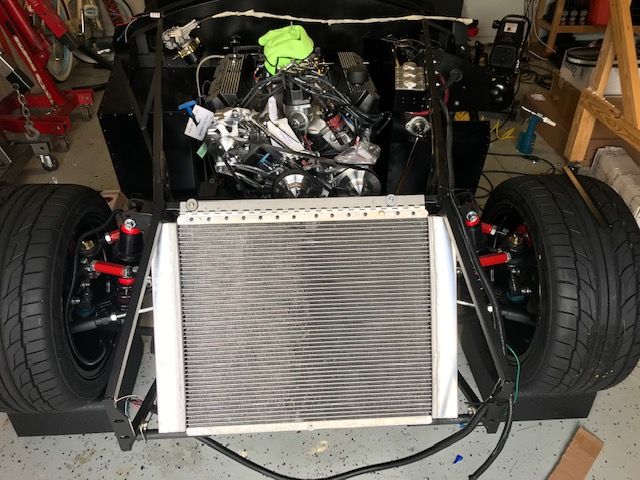
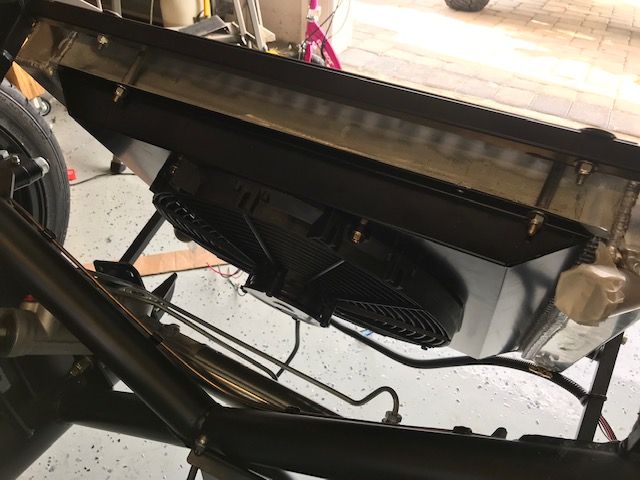
Last edited by cv2065; 04-13-2019 at 09:27 PM.
-
04-13-2019, 09:17 PM
#179
I also got around to buying a couple of new fittings for my Aeromotive fuel line setup in the engine bay. Once the engine was installed, it sat a little to close to the regulator, so needed a 90 degree elbow from Russell to accommodate. Worked great and fuel system is 100%.
-
Post Thanks / Like - 0 Thanks, 1 Likes
-
04-21-2019, 01:10 PM
#180
-
Post Thanks / Like - 0 Thanks, 3 Likes
-
04-21-2019, 01:19 PM
#181
Final connections to my engine wiring. Taking an inspiration from Papa, I took the loom apart, ran the 3 power leads through the firewall to a distribution box that I'll be fastening to the 2" beam just behind the glove box. Wired up another 4 gauge wire and took that from the starter to the box. The smaller starter wire and brown alternator wire (not hooked up), had a separate loom and ran down to the starter. I also had to run the alternator wire by itself, as it was coming up short when reaching the alternator if kept in the FFR loom. Wiring is NOT my favorite thing to do, but seemed to come out great.
I won't secure it completely until I get my underdash panel back in after first start.
Last edited by cv2065; 04-21-2019 at 02:19 PM.
-
Post Thanks / Like - 0 Thanks, 2 Likes
-
04-21-2019, 07:14 PM
#182
Senior Member

Originally Posted by
cv2065
Loom and electrical tape works well and keeps it clean, but electrical tape wants to come loose in some areas. I'm using the 3M Super 33+...thought that was good stuff. Anyone have any suggestions on a good substitute that will stay put?
3M Super 33+ is good stuff. Probably among the best. It sticks well if you don't get crazy stretching it. A little tension is OK, but don't pull too hard or it may eventually loosen itself. I always cut it vs. tearing, which stretches it. Also keep your fingers off the sticky side while using it. It should also be fully stuck down. That bridge stretched across your ground loom by the starter isn't going to hold up. Having said that, many avoid electrical tape as much as possible. Decent stuff like the 3M product can get gummy and messy over time. Even though the Ron Francis harness has a ton of it. I like to use shrink sleeving instead, when possible. Available in every size imaginable, including for the ends of convolute. But takes a little planning.
Last edited by edwardb; 04-21-2019 at 07:18 PM.
Build 1: Mk3 Roadster #5125. Sold 11/08/2014.
Build 2: Mk4 Roadster #7750. Sold 04/10/2017.
Build Thread
Build 3: Mk4 Roadster 20th Anniversary #8674. Sold 09/07/2020.
Build Thread and
Video.
Build 4: Gen 3 Type 65 Coupe #59. Gen 3 Coyote. Legal 03/04/2020.
Build Thread and
Video
Build 5: 35 Hot Rod Truck #138. LS3 and 4L65E auto. Rcvd 01/05/2021. Legal 04/20/2023.
Build Thread. Sold 11/9/2023.
-
04-21-2019, 07:47 PM
#183

Originally Posted by
edwardb
3M Super 33+ is good stuff. Probably among the best. It sticks well if you don't get crazy stretching it. A little tension is OK, but don't pull too hard or it may eventually loosen itself. I always cut it vs. tearing, which stretches it. Also keep your fingers off the sticky side while using it. It should also be fully stuck down. That bridge stretched across your ground loom by the starter isn't going to hold up. Having said that, many avoid electrical tape as much as possible. Decent stuff like the 3M product can get gummy and messy over time. Even though the Ron Francis harness has a ton of it. I like to use shrink sleeving instead, when possible. Available in every size imaginable, including for the ends of convolute. But takes a little planning.
Thanks Paul. Never ceases to amaze me the stuff you guys notice!
I'll be cutting that bridge and addressing it later. I had some cloth electrical tape some time ago and it stuck pretty well. I can't remember the brand, but I'll keep your comments in mind with respect to stretching. That may be the bulk of my issue.
-
04-28-2019, 01:43 AM
#184
-
Post Thanks / Like - 0 Thanks, 3 Likes
-
04-29-2019, 07:57 AM
#185
Waiting on those tubes and headers, went ahead and installed my horns. I didn't deviate from the manual in terms of placement. I did exchange out the FFR provided metal screw with a SS pan head bolt installed from the opposite side to avoid any interference with my Replica Parts radiator panel. I also grinded down the corners on the horn brackets to get them flush with the 3/4" bar. Not sure if that mattered when it comes to body fitment, but took 5 mins. I'll re-route the loomed wiring when I get my lighting configured.
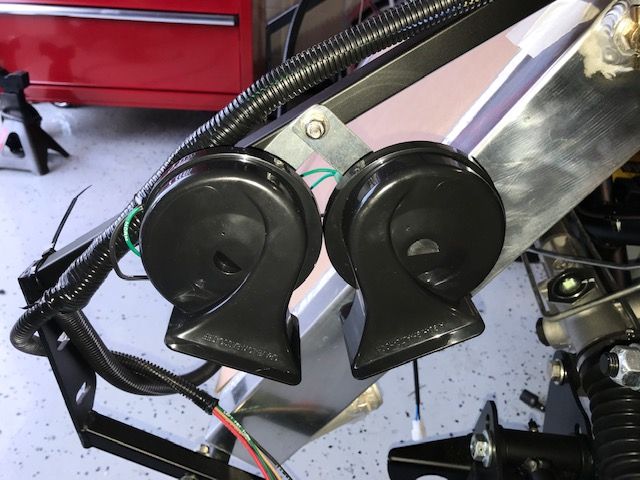
-
05-09-2019, 09:28 PM
#186
-
Post Thanks / Like - 0 Thanks, 1 Likes
-
05-10-2019, 05:00 AM
#187
I can't wait to see that first start video of the BluePrint Beast...
-
05-11-2019, 08:29 PM
#188
-
Post Thanks / Like - 0 Thanks, 2 Likes
-
05-29-2019, 11:35 AM
#189
Looking good! I'll probably need to get the number of your powder coat guy
-
06-02-2019, 06:12 PM
#190
-
Post Thanks / Like - 0 Thanks, 1 Likes
-
06-02-2019, 06:18 PM
#191
Second up was the Moog upper ball joint boots. If you upgrade to the Moog upper ball joints, they are great and thread in nicely. However, using the provided Moog boots is bad news as they are too large and end up pushing in on themselves, then open up and get grease everywhere. Look something like this:
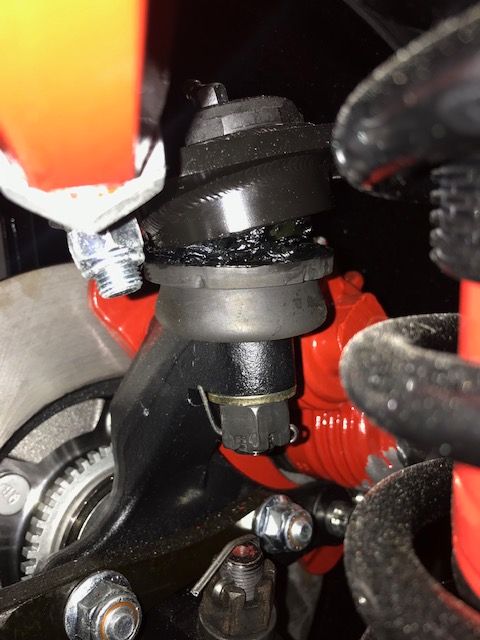
So, based on edwardb's suggestion, I replaced with Energy Suspension 5.13102G Ball Joint Dust Boots. They are less than $10 on Amazon and look fantastic.
After Install:
-
06-02-2019, 06:30 PM
#192
FFR #9380 is ALIVE!
Really glad to have reached this milestone. Just have to say that Josh and Johnny at Blueprint have been VERY responsive to any questions that I've had along the way...yes, even on weekends. Nice work guys!
So, this isn't 'exactly' my first start. If I said it was then Carl (BadASP) would probably throw me under the bus for that, so keeping it real.
Had a few things to work out with setup, and there is still some fine tuning to do, but overall, very satisfied with how things worked out. Good news is that I only had one leak, and that came out of the radiator hose. Everything else is good to go!
Thanks again for all the help from the forum to this point. Very much appreciated!
https://youtu.be/Xhc-DsA50XY
Last edited by cv2065; 06-02-2019 at 06:32 PM.
-
Post Thanks / Like - 0 Thanks, 1 Likes
-
06-02-2019, 06:46 PM
#193
-
06-02-2019, 07:07 PM
#194
I've been planning out my stereo. I know that topic is up for debate, but I've never had a car without one, so the Cobra will get some tunes. I drilled two 1/2" holes on the front right and left sides of the top trunk panel and added grommets for door speaker wiring. I also drilled a 1" hole right in the center of the top trunk panel that will take the amp power and RCA cables through the trans tunnel to the distribution block and BT stereo housed in the glovebox. It will get a grommet as well, it just hasn't arrived yet. Hard to find 1.25" ID grommets locally for some reason.
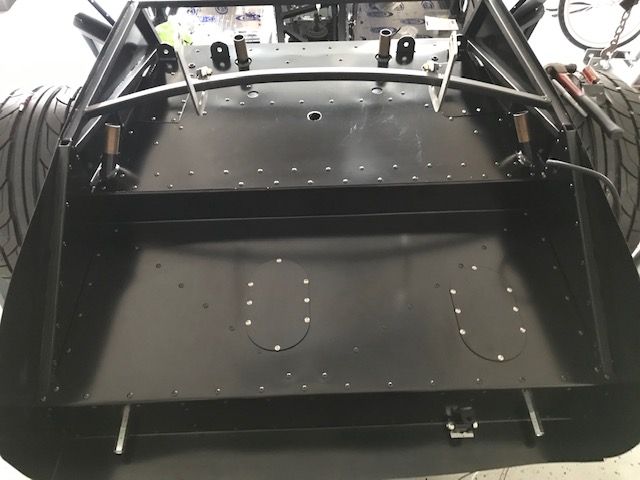
Once the wiring is in, I can start on my rear cockpit panel.
Both of my access panels are removable, as I added 6-32 rivet nuts. I also added another custom panel that is right over my fuel line connections. Probably not necessary, but the fuel line connections are right behind the 2" tube and hard to get to from the outside/bottom. I thought it might make it easier if I ever need to adjust or remove if I can get a wrench on it from the top as well as the bottom.
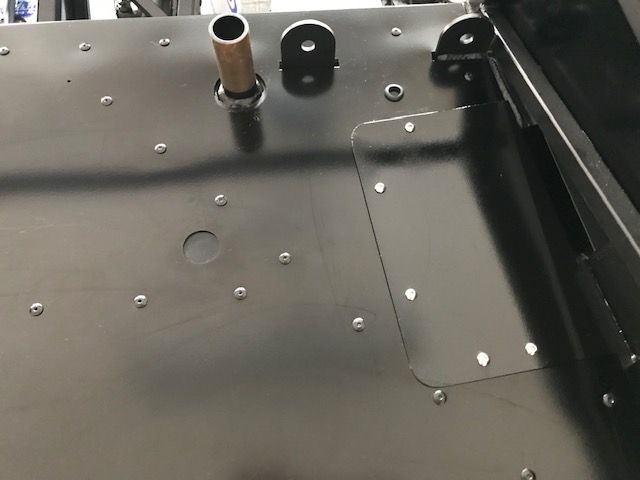

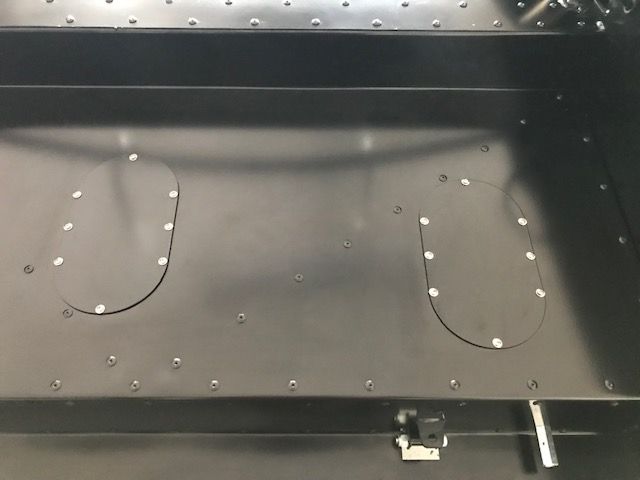
Just a couple of side notes when I was installing the panels. First one is that the center lower trunk panel has to go in first. Just the rivets on the two triangular side panels causes enough interference where the lower panel can't go in. Instructions say that...but that's what happens when you jump ahead!
Also, when installing the lower trunk panel, I totally forgot about the tank strap that the panel has to fit over. So had to get the jack out, support the tank and swap out the bolts allowing the panel to sit flush. Again, rookie move, but it worked out.
Last edited by cv2065; 06-02-2019 at 07:16 PM.
-
06-02-2019, 08:20 PM
#195
Looks like my header ceramic coating is flaming off. Bummer! Already contacted the guy to have these redone, but annoying to say the least.
-
06-02-2019, 09:00 PM
#196
Senior Member
Just wanted to say thanks for the detailed posts. I’ve followed your thread from the start and have found it very helpful for my own build. I’ll be following the stereo portion specifically as this is something I’ll be detailing shortly.
Mike S
-
Post Thanks / Like - 0 Thanks, 1 Likes
-
06-03-2019, 06:33 AM
#197
Nice start! The 427 sounds great!
-
Post Thanks / Like - 0 Thanks, 1 Likes
-
06-03-2019, 07:08 AM
#198
Not a waxer

Originally Posted by
cv2065
Looks like my header ceramic coating is flaming off. Bummer! Already contacted the guy to have these redone, but annoying to say the least.
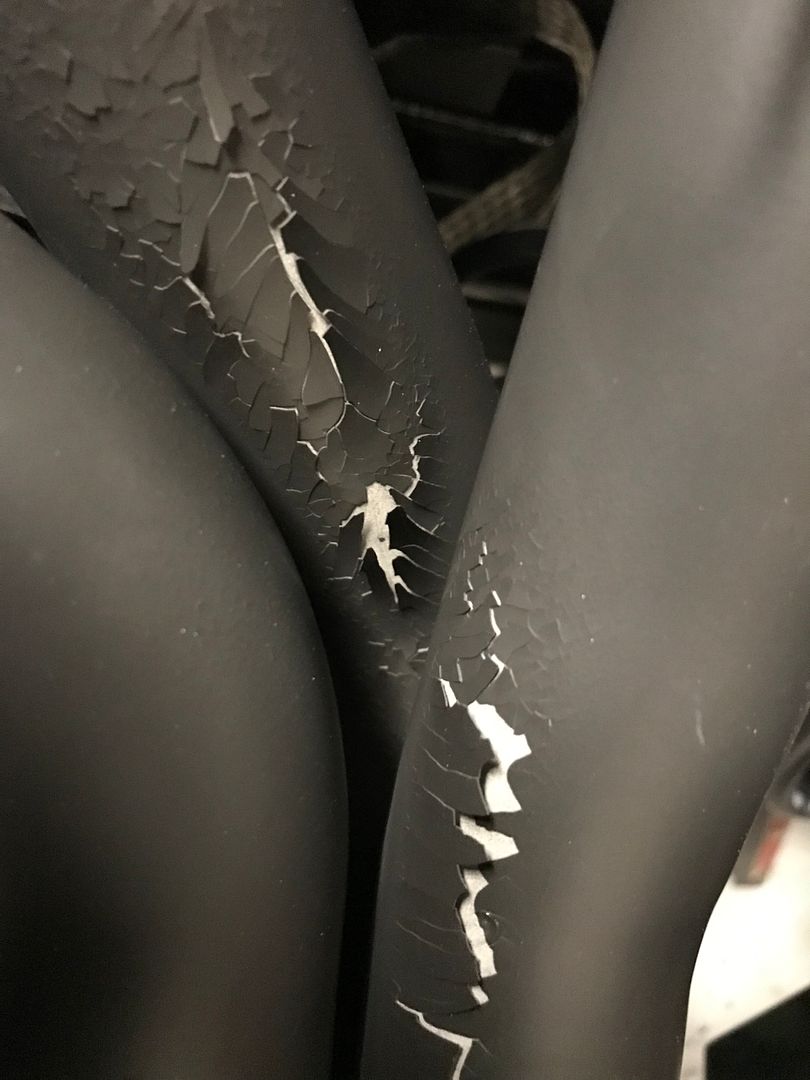
Well that's ugly
What does he intend to do differently this time?
Jeff
-
06-03-2019, 08:31 AM
#199

Originally Posted by
Jeff Kleiner
Well that's ugly

What does he intend to do differently this time?
Jeff
Good question. I had to call him a couple of times to get these done. Not sure if he was backed up or what, but when I showed up they were just coming out of the oven, so maybe they were rushed during the baking process. I'll be reviewing with him when I drop off this week. Most likely will take my exhaust to another guy that's just down the road from him.
-
06-03-2019, 09:38 PM
#200

Originally Posted by
cv2065
Really glad to have reached this milestone. Just have to say that Josh and Johnny at Blueprint have been VERY responsive to any questions that I've had along the way...yes, even on weekends. Nice work guys!
So, this isn't 'exactly' my first start. If I said it was then Carl (BadASP) would probably throw me under the bus for that, so keeping it real.

Had a few things to work out with setup, and there is still some fine tuning to do, but overall, very satisfied with how things worked out. Good news is that I only had one leak, and that came out of the radiator hose. Everything else is good to go!
Thanks again for all the help from the forum to this point. Very much appreciated!
https://youtu.be/Xhc-DsA50XY
Awesome, CV! Congratulations!! Really happy for you.
-
Post Thanks / Like - 0 Thanks, 1 Likes