
Visit our community sponsor

Thanks:
0

Likes:
0
-
Member
-
Member
Since mine were going to be removable for the Exhaust Shootout I welded them to a base plate with a bolt for attachment but you would weld it straight onto the pipe. These were made with 18-gauge tubing but I would suggest 16 gauges. Once you have the patterns you can use the same paper pattern technique as I used for the How-To Super Port J-Pipes to transfer the patterns to the metal pieces.
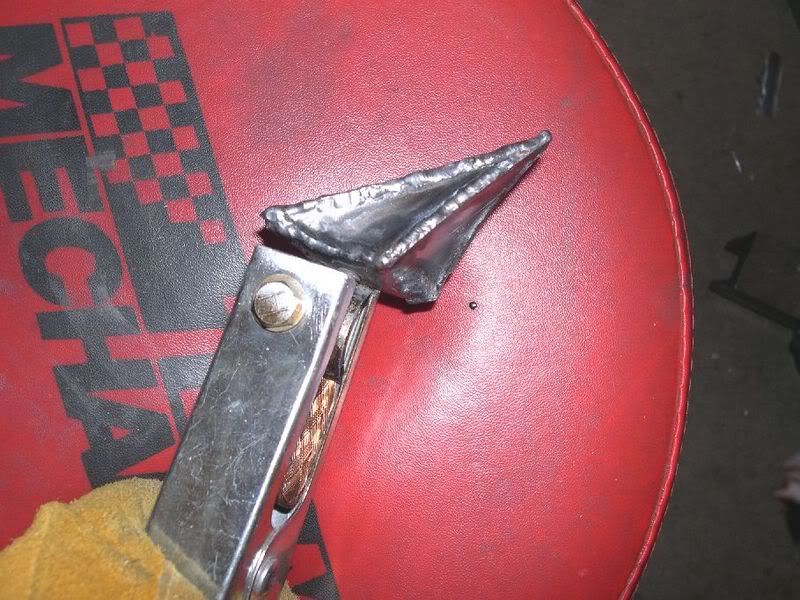
-
Member
-
Member
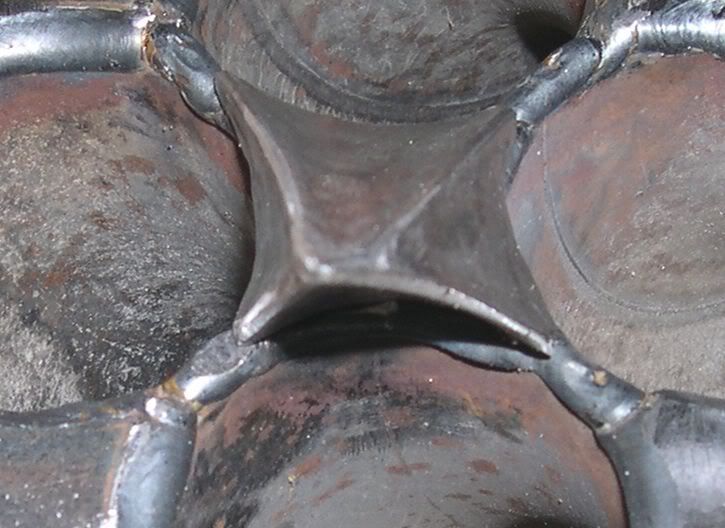
Here is a pic after the dyno runs. You can see the tack welds at the corners for the temporary installation. For a permanent installation they should be completely welded up at the seams and smoothed out.
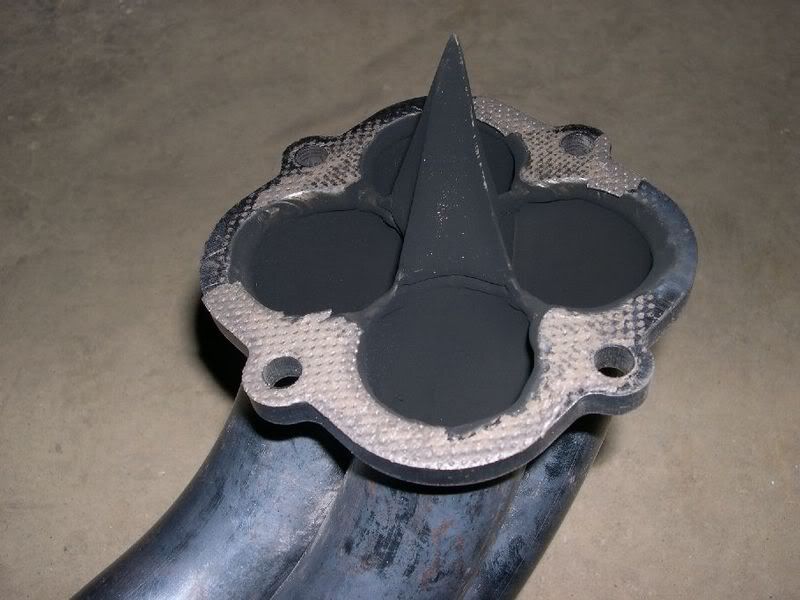
Cheers, Rod
Posting Permissions
- You may not post new threads
- You may not post replies
- You may not post attachments
- You may not edit your posts
-
Forum Rules

Visit our community sponsor